AK-9
Introduction
Compared to piston engines, jet engines have an exceptionally good power-to-weight ratio and are easier to integrate into the fuselage of a glider than a piston engine due to their small dimensions. A glider can therefore be equipped with a homecoming aid at a low additional weight, which has a good efficiency even at high speeds and is much easier to operate in the event of an outlanding, starts up more reliably in principle and generates far less drag than a stationary propeller with engine. The aim of the project was to equip a DG 1000 with a jet engine and to optimize this propulsion system.
Implementation
The project idea had already existed for several years at the Akaflieg Karlsruhe, but progress was rather modest in the first few years due to a lack of funding. However, thanks to the generous support of Prof. Dr. Wittig and the Institute for Thermal Fluid Machinery, the project made significant progress from 2008 onwards. When the DG-1000 was built, it was already equipped with a tank and an engine box to prepare it for installation. A corresponding design based on the DG-1000T engine mount was developed so that the turbine could be retracted into the fuselage when not in use. In 2010, several factors led to the decision to use a different engine than the one originally intended for installation (PBS TJ100). The choice fell on an engine from the model construction sector, type “AMT Titan” with 400N thrust. The company PSR Jet System, which wanted to establish jet engines as a propulsion system in gliders, supplemented this engine for our purposes with the necessary hardware to be used in the glider. These are primarily a modified engine control and monitoring system including a cockpit instrument, a modified fuel system and a containment system that prevents parts from leaving the engine casing and causing damage to the aircraft in the event of a compressor or turbine rupture. PSR Jet System was able to draw on the hardware and experience of the PSR T01, which was already undergoing type certification at the time.
In 2010, the important course was set for the project and the design and development phase was completed. Shortly before Christmas 2010, we received the system with turbine and all its components from Holland. Work then began on installing the engine in the DG-1000, adapting and expanding the electrical system so that the cockpit instrument could be used to control the extension. In addition, they wanted to obtain data on the tail temperature at 8 measuring points during the flight, which is why a data acquisition system was developed and installed to display the highest temperature in the cockpit. At the same time as the installation, trials and test series were carried out to obtain provisional certification. The successful first flight then took place at the 2011 summer meeting. We were satisfied with the handling and the achievable horizontal speed, but the climb rates fell short of expectations.
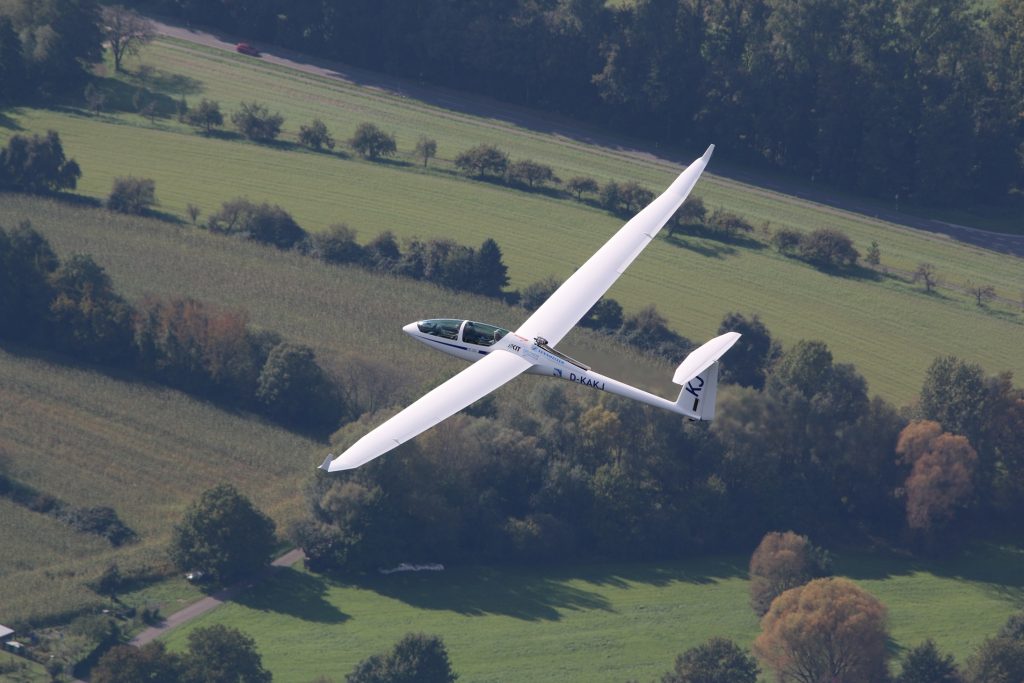
Optimization
From the outset, a sub-goal of the project was to optimize the turbine drive system in the glider for this application. There were already a few small gas turbines in single-seater gliders, but the efficiency and noise emissions of the propulsion system were definitely in need of improvement. The basic problem with small gas turbines, apart from the low thermal efficiency (of just under 18% for the engine used), is the unfavorable exit speed of approx. 500 m/s for the flight speed of a glider, which results in a very poor propulsion efficiency of approx. 13% at 100 km/h. The overall efficiency is around the same as that of a single-seater glider. The overall efficiency is therefore in the region of approx. 2%. The challenge was therefore clear: reducing the exit speed while increasing the volume flow. At this point, a small fan engine would have been the most elegant solution, but also a very complex one, which is why it was decided to focus the research on a suitable ejector. An ejector is a suitable tube in which air is accelerated through momentum exchange, while the core jet is decelerated as a result. At the same time, the aim was to reduce noise emissions.
Through theoretical preliminary work, many series of tests on a specially equipped test rig at the Institute for Thermal Turbomachinery and the subsequent flight tests, a noticeable improvement in efficiency and flight performance was achieved and demonstrated, at least in terms of propulsion efficiency. The propulsion efficiency at 100 km/h could be increased by 10% to 23%, which corresponds to an increase in climb rate of approx. 0.2 m/s. However, the best climb rate was achieved at approx. 130 km/h. With regard to noise emissions, the approach chosen was to line the ejector with a metal laminate (“SilentMetal”), which is coaxial in a tubular shape and at a defined distance from the outer wall of the ejector. This should allow the sound to penetrate through the SilentMetal and die out between it and the outer wall of the ejector. Ultimately, this did indeed contribute to a reduction in noise in certain areas, but the length of the ejector was too short for the expected overall reduction. Noise emissions were reduced by 3 dB (SPL), particularly in the area to the side of the turbine.
Project Finalization
Further flight tests were carried out in 2021 and 2022, but these showed that the noise specifications required for single-unit certification could only be met with a reduction in power. As certification was not possible with the current turbine, it was decided with a heavy heart to remove the engine and concentrate on the current project, the AK-X.
Technical Data
Wingspan | 18 / 20 m |
Wing Area | 16,72 / 17,51 m2 |
Aspect Ratio | 19,38 / 22,84 |
Fuselage Length | 8,66 m |
Unladen Weight | 465 kg |
Max. Take Off Weight | 750 kg |
Max. Wing Loading | 44,9 / 42,8 kg/m2 |
VNE in Still Air | 270 km/h |
Lowest Sink Rate (Single-Seat) | 0,51 m/s |
Glide Ratio at MTOW | 45 |
Turbine Specific: | |
Best Climb (MSL) | 0,8 m/s |
Speed at Best Climb | 130 km/h |
Max. Horizontal Airspeed | 170 km/h |
System Weight Turbine + Peripherals | 12 kg |
Fuel Supply | 30 l |
Range | approx. 100 km |