AK-2
The AK-2 project is probably Akaflieg Karlsruhe’s most extensive and ambitious project. After successes with the AK-1 motor glider, the decision was made in 1973 for an even larger and more powerful machine, based on one of the best gliders of the time, the “Glasflügel 604”.
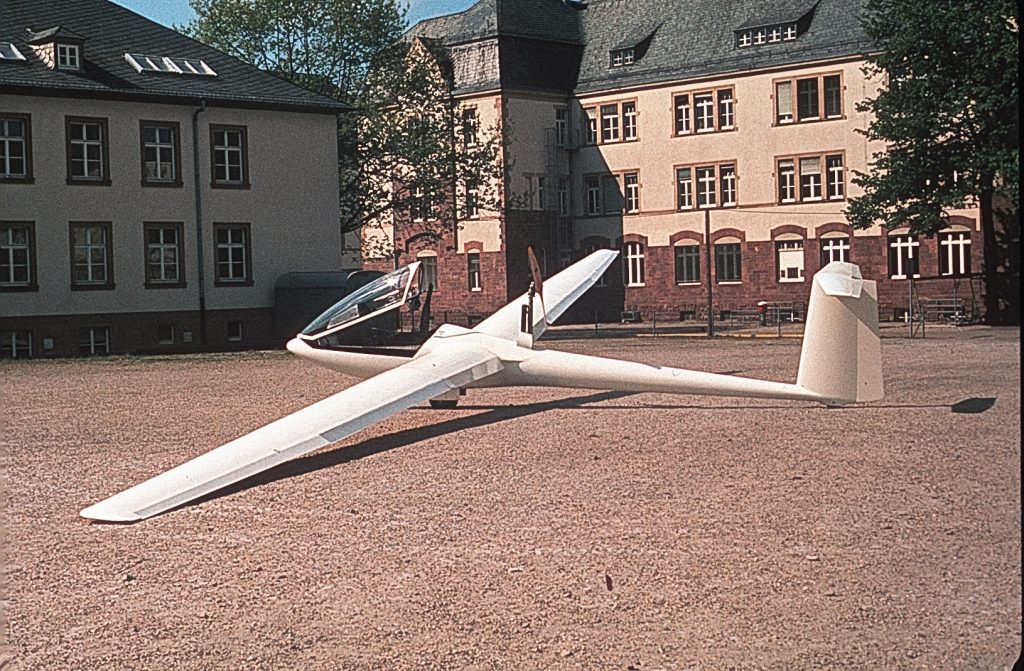
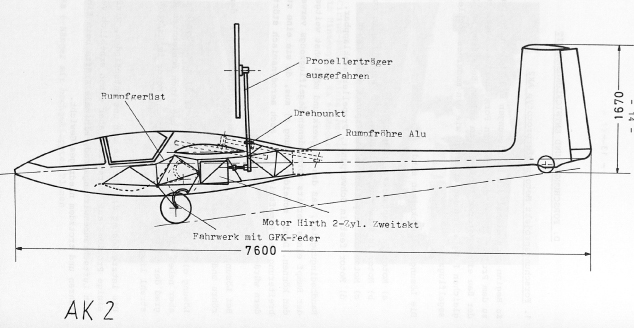
Over a total of 16 years (see timeline below), a large number of engines, drives, functional models, engine test benches and complex electronic control systems were developed and tested, and wings and tail units as well as a fuselage mock-up were built.
Comparisons with today’s state of the art show just how far ahead of its time this project was:
- Modern motor gliders such as the DG-800 use a toothed belt drive, with the engine remaining in the fuselage
- A tubular steel construction for mounting the engine and landing gear is used, for example, in the Stemme S10.
- The engines used, such as those from ROTAX, are liquid-cooled
- A central electronic control unit takes over the entire engine management, including extending and retracting the boom
Considerable technical difficulties, but also internal disputes within the group ultimately meant the end for the AK-2, which (unfortunately not airworthy) had already been parked in front of our workshop (see picture) and never took to the air.
Please send any comments, questions or suggestions on this topic, which even after all this time has led to heated discussions in some of the Alumni camps, to Dirk Münzner (Spatzl), who designed this compilation.
Timeline
27.10.1973
- Decision in favor of a motor glider at the general meeting
1975
- First version of the fuselage frame made of steel
- Fuselage tube made of aluminum
- 720cc Hirth 2-T
- Exhaust optimization
- Propeller calculation with own program
- Lack of space in the fuselage
- Modified aileron overlay mechanics
- Modified landing gear with GRP springs
1979
- Another version of the star wheel kinematics
- Spring-loaded claw clutch
- New drive: Volvo 70 hp boat engine
- Test runs with toothed belt
- Toothed belt fails after a short period of operation
- Hydraulic drive < 400 bar not considered feasible
- Boom with two angular gearboxes from ZF
- Boom kinematics
- Fracture analyses with force transmission elements
- Construction of tail unit
- Cockpit mockup (student research project)
- Further fittings from ‘Glasflügel’
1981
- Hannover Messe
- Installation of control unit in mockup fuselage
- Bonding of the fuselage shells and modification
- Adaptation of the framework
- Modification of landing gear kinematics
- Assembly of angular gear
- Assembly of boom kinematics
- Canopy production
- Completion of cockpit
- Modification of electrics
- Further development of the retractable spur
- Conception of a 3-cylinder hydraulic radial engine for motor gliders
1982
- Modification of control system due to space problems
- Center of gravity calculation results in excessive tail weight
- Problems with Volvo boat engine: crankshaft too weak
- Lubrication problems on the upper outrigger gearbox
- Design of a CFRP boom
1984
- Construction of a new engine test bench
- Investigation of cooling problems
- Experience report by Nadim
- Further development of the idea of a hydrostatic drive
- Start of construction AK-5