AK-7
Summary
As part of the AK-7 project, the physical processes during a winch launch were mapped using a theoretical model. This model was then verified by a computer-aided recalculation and further adapted to reality. The basis for this recalculation was measurement data from real, measured winch launches. As a result, in addition to the model, further findings on the processes involved in winch launches and a measurement method for measuring winch launches were presented.
Motivation and Goals
The starting point for the project was the desire to automate winch launches as optimally as possible in order to increase the achievable height for the launch as much as possible and, above all, to reduce the variation in launch heights that often occurs in everyday towing operations.
However, it quickly became clear that not enough was known about the physical processes involved in winch launches. The aim of the AK-7 project was therefore to determine the relevant influencing variables and correlations during the launch of a glider on the winch.
With the knowledge gained, it should be possible to create general rules that could be used not only for automation and optimization, but also for improving the safety of winch launches and for the design and construction of a glider launch winch.
Creation of the Theoretical Model for the Winch Launch
First, a theoretical model was created and implemented as a calculation method on a PC. The model results from the consideration of the most important forces acting on the aircraft, namely its weight, lift and drag, as well as the rope force. In the course of the project, further influencing variables were gradually taken into account in the theoretical analysis and the model was thus continuously refined.
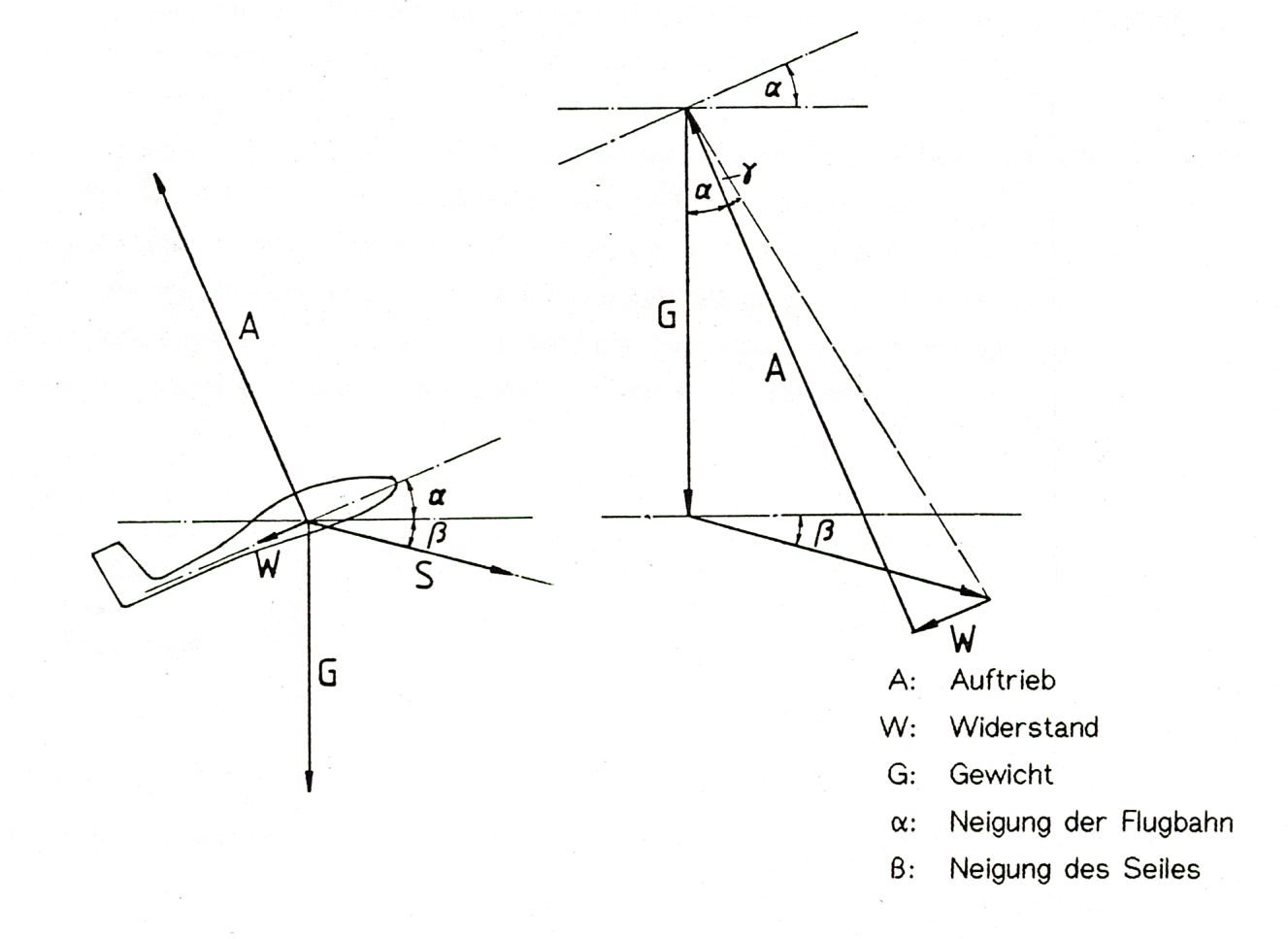
Simplified balance of forces on the aircraft during winch launch
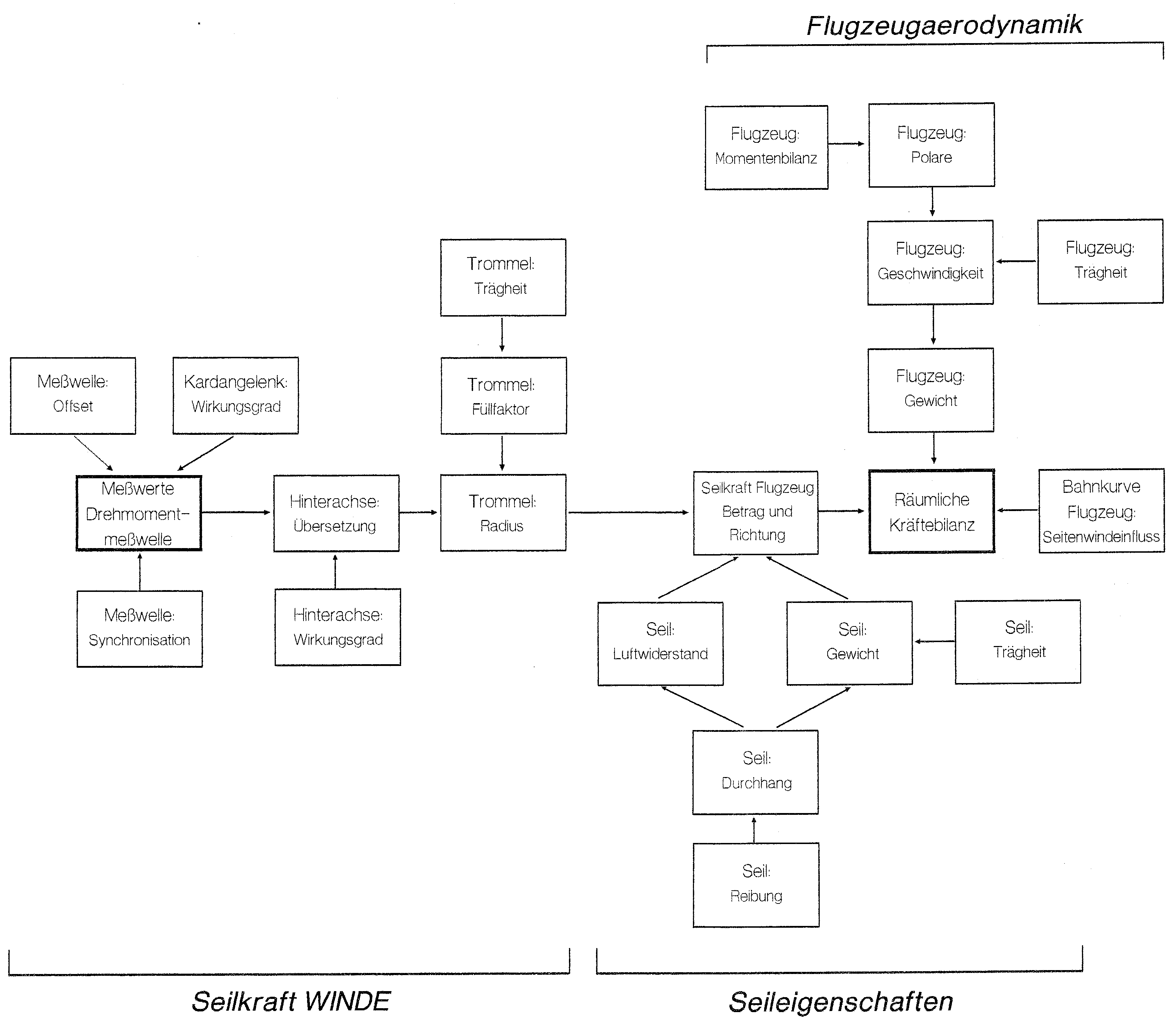
Development of a Measurement Method
In order to clarify the accuracy with which the theoretical model describes reality despite the simplifications made, the trajectory of the glider taking off and the maximum take-off height of real take-off procedures had to be measured. At the same time, all variables that served as input values for the later recalculation, such as the course of the rope force and the retracted rope length, had to be recorded.
Two electronically controlled and motorized cameras were used to measure the flight path. During the take-offs, the cameras took continuous series of photos from fixed points along and across the flight path, recording the positions of the aircraft taking off at regular intervals. The flight path was then determined from the series of photos using a photogrammetric process.
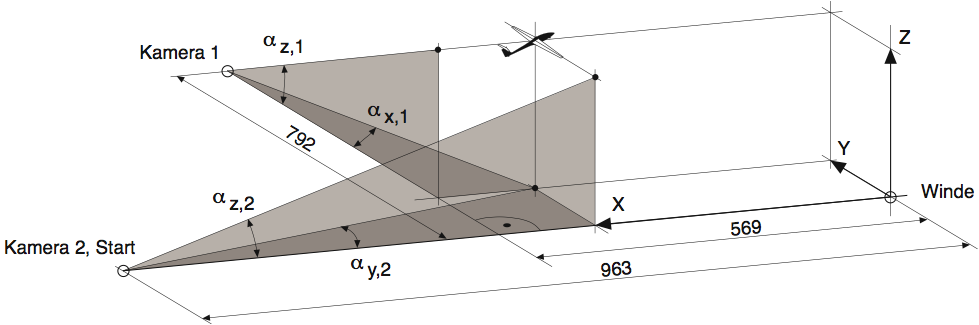
Parallel to measuring the flight path, the torque curve in the winch’s drive train, the drum speed and the position of the azimuth pulleys, which are located at the rope’s entry point into the winch, were recorded. The torque shaft and the speed display of the cable drums (also known as the “omega visualizer”), which were already installed in the Akaflieg AFK-3 winch, were used for this purpose.
An electronic measuring interface developed for the project and an ATARI PC with self-developed software were used to record and store the measured values. The required rope force curve was then calculated from the measured torque curve as part of the recalculation. In order to start the two cameras and the recording of the measurement data in the winch at the same time, the cameras and the measuring device in the winch were electronically synchronized via a radio signal
Measurement of Real Winch Launches
From 1988 to 1994, numerous winch launches were carried out at the Karlsruhe-Forchheim airfield, “EDTK” (now the Karlsruhe Trade Fair Center) using the measurement method described above.
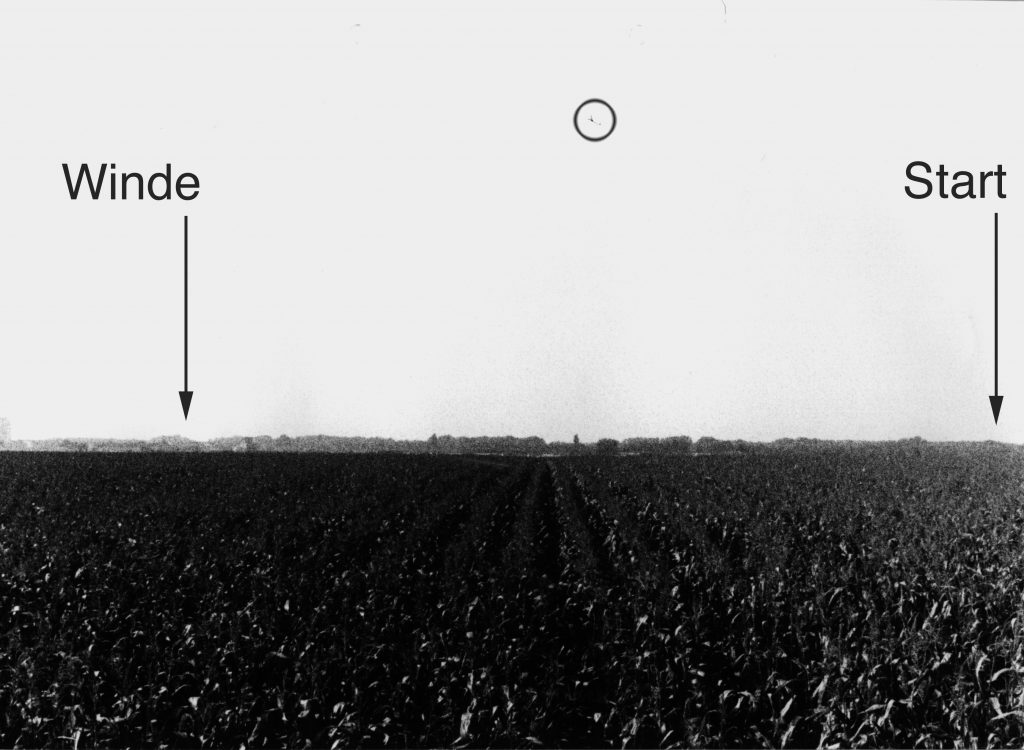
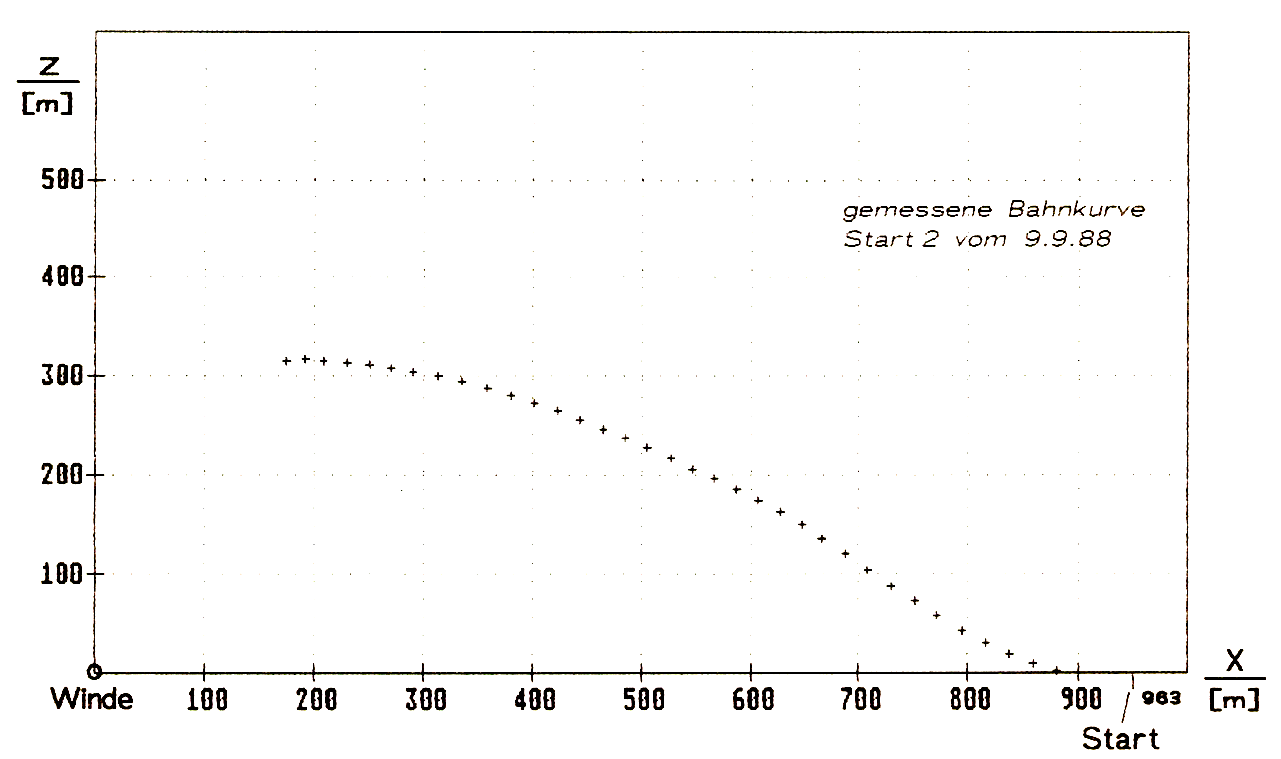
The values measured on the winch for the torque, the retracted cable length and the position of the azimuth pulleys were used together with other parameters (such as the aerodynamic data of the aircraft and the cable) as input values for the recalculation.
Recalculation to Verify or Adjust the Theoretical Model
A recalculation was carried out for several measured take-offs, in which the trajectory and the corresponding maximum take-off altitude were calculated from the above-mentioned input values. To assess the accuracy of the model compared to reality, the calculated trajectory and take-off height were then compared with the measured trajectory and take-off height for the same take-off. This was to ensure that all significant influences and processes during the winch launch were captured and correctly mapped by the theoretical model.
The recalculation was carried out in three phases:
- Acceleration of the aircraft from the start of take-off to lift-off
- Initial climb phase until the rope is completely lifted off the ground
- Remainder of the climb phase until the rope is released
The core of the recalculation was an iterative calculation method that calculated an energy balance for the aircraft and cable system at fixed time intervals (usually 0.1s) from the start of the take-off to the release of the cable and compared it with the work performed by the winch in this interval.
In this way, the energy applied by the winch could be related to the useful energy on the aircraft (kinetic and potential energy) and lost energy (e.g. due to friction).
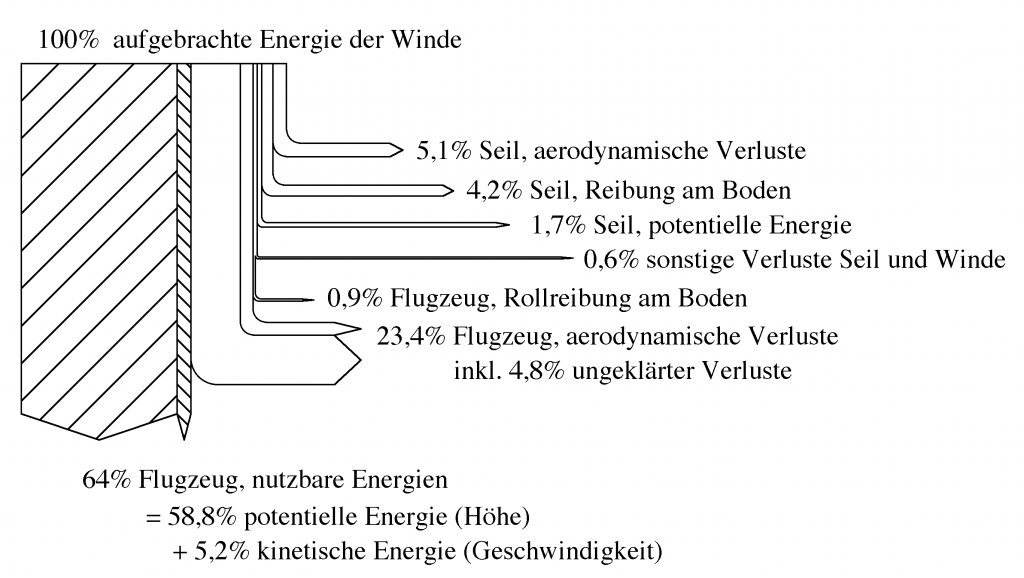
Results
The recalculations showed that the calculated maximum take-off heights matched the measured take-off heights with good accuracy. The accuracy of the recalculation (and thus that of the underlying theoretical model) was just under 8% in relation to the measured useful energy “height above take-off”. The sequence of the winch launch could therefore be reproduced with sufficient accuracy by the theoretical model developed.
The recalculation also showed, among other things, that the flight path of the starting glider essentially corresponds to the course of a cosine function if it is considered transverse to the direction of flight.
An interesting side result of the recalculation was that the lift coefficient (cA value) of the glider was never greater than 1.02. This means that it was never possible to reach the maximum cA value of around 1.33 and thus the critical limit for stalling, despite the tailplane being fully retracted.
Project Team
The AK-7 project was a joint effort in which numerous Akaflieger were involved. Most of them, however, only for a limited period of time in order to complete specific subtasks. For example, in the development of the measurement interface by Franz Haas or in the measurement campaigns at the airfield. The project was driven and led by Tobias Hoffstetter and Gerhard Arnold Seiler, who played a key role in developing the model and carrying out the recalculation.