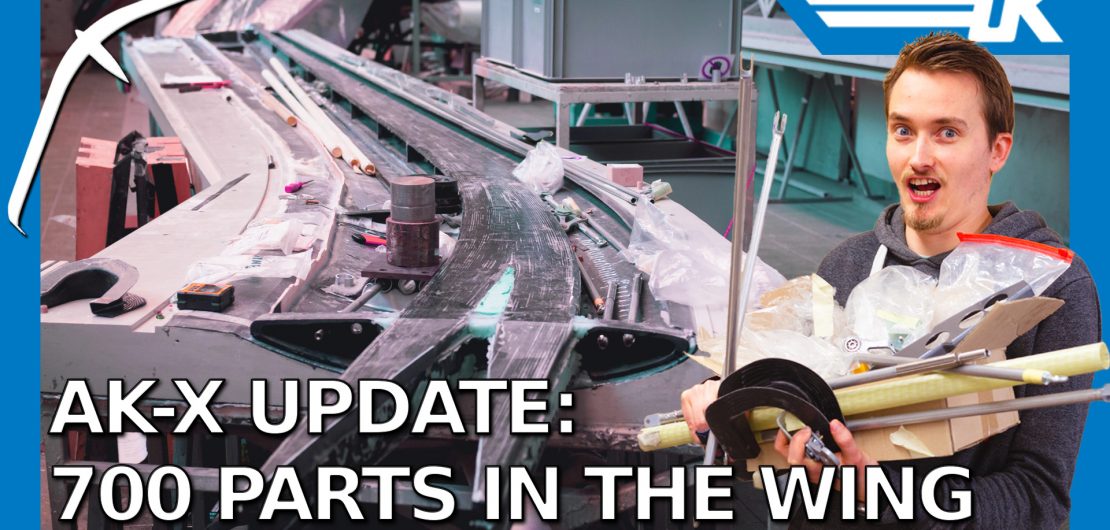
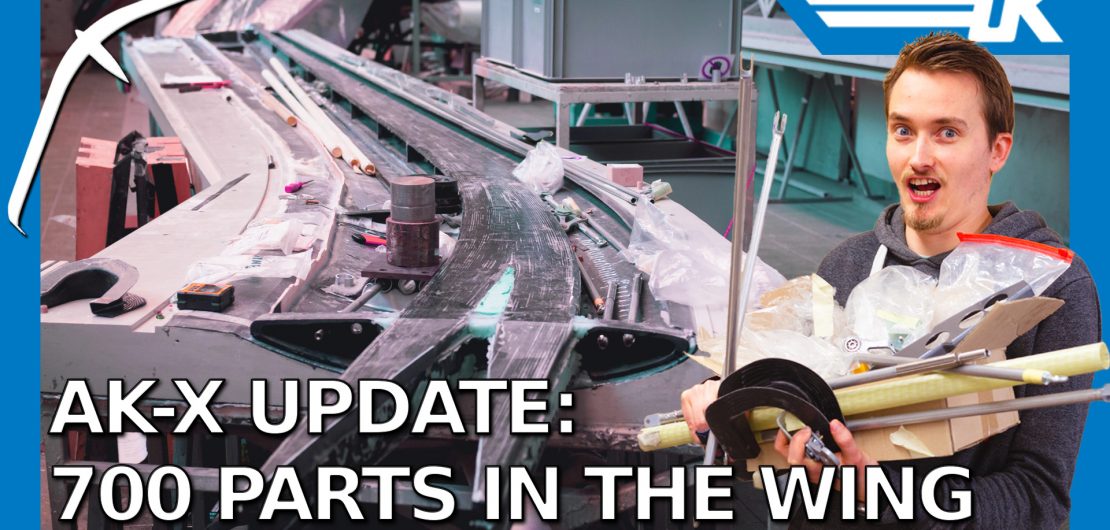
Wir haben uns eine eine 360° Kamera gegönnt. Damit gibt es jetzt noch coolere Videos vom AK-X Modell.
Zuletzt wurde getrudelt:
Weit über 1000 Arbeitsstunden sind in den Bau von Bruchwinglet, Flügelsteckungsdummy und Versuchsaufbau, Lastfallanalyse und -Auswahl und die Organisation und Planung des Wingletbruchversuchs geflossen.
Nun haben wir diesen wichtigen Meilenstein erfolgreich hinter uns gebracht!
Im Vorfeld war trotz seit längerem fertiger Bauteile (siehe Warten auf Wingletbelastung) noch Einiges vorzubereiten: Neben der Abstimmung mit dem Luftfahrtbundesamt (LBA) und der Versuchsanstalt für Stahl, Holz und Steine (VAKA) am KIT, wo wir den Versuch durchgeführt haben, haben Planung und Vorbereitung des Versuchsaufbaus viel Zeit in Anspruch genommen. Derart umfangreiche Versuche bieten viel Raum für unerwartet auftretende Probleme. Aufgrund des begrenzten Zeitfensters für die Nutzung der Versuchshalle – ein Tag für den Aufbau sowie ein weiterer für Durchführung und Abbau – war es entsprechend wichtig, auf alle Eventualitäten vorbereitet zu sein.
Der Aufbau funktionierte – auch dank der fachkundigen Unterstützung durch die Mitarbeiter der VAKA – problemlos. Zunächst montierten wir das Lasteinleitungsgeschirr an der Prüfmaschine und unser Einspanngestell am Nutenboden. Mit dem darauf gesteckten Bruchwinglet wurde dann alles zueinander ausgerichtet. Um den gesamten Aufbau haben wir schließlich eine Box aus Dämmelementen aufgestellt. Nach der Befestigung von Kameras, Sensoren und dem Aufbau der Heizanlage wurde der gesamte Aufbau über Nacht aufgeheizt, um alle Bauteile am nächsten Morgen zuverlässig auf die Versuchstemperatur von 54 °C durchgewärmt zu haben.
Am nächsten Morgen ging es ans Eingemachte:
Zuerst wurden mittels Handkraftmesser einige zusätzliche Lastfälle getestet:
An der Wingletspitze dominieren die von der Bauvorschrift vorgegebenen Handkräfte von 15 daN, die das Winglet in alle Richtungen ertragen können muss. Außerdem wurde die bei einer Drehlandung auftretende Kraft am Bodenberührungspunkt des Flügels – also nahe dem Knick des Winglets – getestet. Aufgrund der hohen erwarteten Sicherheiten haben wir diese Lasten unter den wachsamen Augen unseres LBA-Projektbetreuers bis zu einem Sicherheitsfaktor von 1,5 aufgebracht und gehalten. Der Erfolg dieses ersten Teils des Bruchversuchs wurde bestätigt, als wir danach keine bleibenden Deformationen feststellen konnten.
Schließlich ging es mit dem eigentlichen Versuch los: Der dimensionierende Lastfall für das Winglet ist eine seitliche Böe bei hoher Geschwindigkeit. Durch die große Fläche des vertikalen Teils wird dabei das gesamte Winglet sowie die Steckung zum Flügel stark beansprucht. Auf der Seite, auf der das Winglet durch die Luftkraft nach außen gebogen wird, treten durch die Geometrie noch größere Lasten im Knick- und Steckungsbereich auf als bei Biegung nach innen. Daher wurde im Bruchversuch die Biegung nach außen getestet. Um die Last durch die vertikal arbeitende Prüfmaschine direkt einleiten zu können, ist das Winglet im Versuchsaufbau so gedreht, dass dessen vertikaler Teil annähernd horizontal ist. Damit die Last im verformten Zustand, nahe der erwarteten Bruchlast, möglichst genau den tatsächlichen Bedingungen entspricht, wurde der Winkel des unbelastet eingespannten Zustands entsprechend angepasst.
Das Winglet wurde zunächst bis zur sicheren Last von j=1 belastet, das entspricht in diesem Fall etwa 1800 N. Bis dorthin darf natürlich nichts kaputtgehen, sodass jedes plötzliche Knacken oder Knallen ein bisschen Nerven kostet, auch wenn es durch leichtes Verrutschen oder Setzen des Lasteinleitungsgeschirrs ausgelöst wird. Nach dem folgenden Entlasten konnten wir das Winglet noch ein letztes Mal in intaktem Zustand begutachten und uns durch die Kraft- und Weg-Aufzeichnungen der Messaufnehmer davon überzeugen, dass keine bleibenden Deformationen auftreten.
Ab dann ging es nur noch „nach oben“. Alle vorgeschriebenen Lasten müssen im Versuch mindestens 3 Sekunden lang getragen werden. Mit Pausen bei den entsprechenden Sicherheitsfaktoren von j=1 und j=1,5 (mindestens nachzuweisende Bruchlast) ging es weiter an j=1,725 (Nachweis der Dauerfestigkeit) vorbei dem sicheren Bruch entgegen. Gelegentliches Knacken wies darauf hin, dass trotz steigender Last nun erste Schäden auftraten. Bei j=2,1 wurde ein erster äußerlich erkennbarer Schaden, nämlich Beulen an der Endleiste im horizontalen Teil sichtbar. Dennoch konnte die Last weiter gesteigert werden, bis schließlich bei j=2,2 die Schale an der Nasenleiste im Horizontalteil versagte und auch der Holm brach.
Auch im entlasteten Zustand hat das Bruchwinglet noch erstaunlich fest zusammengehalten, sodass wir den gesamten Aufbau wie auf der Hinfahrt transportieren konnten, nur mit ein paar offensichtlichen Schönheits- (und Struktur-) Fehlern. Um die Bruchstelle genauer analysieren zu können haben wir das Winglet schließlich noch aufgesägt.
Aktuell läuft die genaue Analyse und Nachweisführung. Mit dem erfolgreichen Nachweis der in der Bauvorschrift geforderten Sicherheiten steht dem Bau der fliegenden Winglets dann nichts mehr im Weg.
Ein großer Dank gebührt der Versuchsanstalt für Stahl, Holz und Steine am KIT! Durch die Nutzung der professionellen Prüfmaschine und Messtechnik und insbesondere auch durch fachkundige Beratung seit der frühen Planungsphase haben deren Mitarbeiter die Durchführung dieses für uns ziemlich komplexen Versuchs erst ermöglicht.
Die Schwerpunktlage spielt bei der AK-X wie bei jedem Segelflugzeug eine wichtige Rolle. Sie beeinflusst sowohl Flugeigenschaften als auch Flugleistung und will somit optimal eingestellt sein. Dafür kommt ein Trimmballast im Heck des Rumpfes zum Einsatz, dessen frisch abgeschlossene Konstruktion nun zur Fertigung bereit ist.
Eine Besonderheit bei unserem Nurflügel ist, dass der Pilot genau im Schwerpunkt des Flugzeuges sitzt. Dadurch entfällt die üblicherweise notwendige Kompensation der unterschiedlichen Pilotenmassen.
Allerdings ist es trotzdem notwendig, verschiedene Schwerpunktlagen erproben und einstellen zu können. Da der Flieger voraussichtlich im vorderen Bereich etwas schwerer wird als in der ursprünglichen Auslegung abgeschätzt, muss sowieso im Heck zusätzliches Gewicht hinzugefügt werden. Ein Trimmgewicht an der hinteren Rumpfspitze wurde schon zu Beginn der Konstruktion vorgesehen und soll mit variablem Ballast für Einstellungsspielraum sorgen.
Die Anforderungen sind wie folgt: Das Gewicht soll zwischen 5 und 30 kg in Stufen einstellbar sein. Der Schwerpunkt des Trimmgewichts soll so weit hinten wie möglich liegen und bei jeder Beladungskonfiguration die gleiche Außenkontur besitzen. Aus diesen Spezifikationen entwickelten wir dann das Trimmballastkonzept.
Um das hohe Maximalgewicht von 30 kg zu erreichen, muss ein Teil des Trimmballastes nach vorn in den Tank des Wasserballasts hineinragen. Abgedichtet wird dieser Übergang durch einen O-Ring, welcher zwischen dem hintersten Spant des Rumpfes und der Grundplatte des Trimmgewichts montiert ist. Durch den Wasserkontakt haben wir uns für Edelstahl entschieden, damit es nicht zu Korrosion kommt. Die Grundplatte wird dauerhaft am Flugzeug verbleiben.
Ein Rohr, welches in den Wasserballast hineinragt, kann mit 8 Bleigewichten à 2kg bestückt werden. Um ein Verrutschen der Bleigewichte zu verhindern, werden diese an einem Rundstab verschraubt. Durch Abstandshalter können die einzelnen Bleigewichte auch in einem nicht vollständig gefüllten Rohr gesichert werden. Die Bleigewichte verfügen über je zwei Langlöcher, wodurch der Ausbau mit einem Ausziehwerkzeug erfolgt.
Ist das Rohr gefüllt, erfolgt die Montage der Trimmgewichtspitze, welche ein Gewicht von ungefähr 10 kg besitzt. Auch dieses Bauteil wird über den Rundstab gesichert, aber nun mit einem kleineren Durchmesser. Dadurch ist das Gewinde, mit dem die Bleigewichte gesichert werden, kürzer und ein Wechsel der Bleigewichte deutlich schneller. Um die Trimmgewichtspitze zu zentrieren und gegen Verdrehen zu sichern, gibt es eine Struktur auf der Grundplatte, die in das Trimmgewicht eingreift. Zudem besitzt diese Struktur auf der Grundplatte die Funktion, die Kontaktfläche zwischen Rohr und Grundplatte zu vergrößern.
Die gesamte Konstruktion wird durch eine Verkleidung aus Faserverbundwerkstoffen aerodynamisch abgedeckt. Die Befestigung der Verkleidung erfolgt durch in der Seite eingeschraubte federgelagerte Bolzen. Somit ist eine Demontage der Verkleidung und Änderung der Gewichtskonfiguration auf dem Flugplatz relativ einfach und schnell möglich.
Die Grundplatte und die Trimmgewichtspitze werden aus Rundmaterial aus dem Vollen CNC-gefräst. Andere Bauteile, wie das Rohr, der Rohrdeckel oder der Rundstab können auf Maschinen der Akaflieg bearbeitet werden.
Für den Guss der Bleigewichtscheiben haben wir uns für eine zweigeteilte Form aus Hochtemperatursilikon entschieden. Hierfür werden Formen per FDM-3D Druck gefertigt. Diese werden mit Silikon ausgefüllt und härten zur Vermeidung von Luftblasen unter Unterdruck aus. Anschließend wird die Form zusammengesetzt und mit Blei ausgegossen. Danach kann die Form wiederverwendet werden.
Die Verkleidung wird auf das montierte Trimmgewicht mit Trimmgewichtspitze laminiert. Dadurch ist ein perfektes Anliegen der Verkleidung auf der Grundplatte gewährleistet.
Die Baugruppe ist also für einen „bloßen Klumpen Blei“ relativ aufwändig, durch die ausgeklügelte Konstruktion mit einfacher und sicherer Anpassbarkeit des Ballasts erwarten wir aber auch einen großen Nutzen für Flugerprobung und Normalbetrieb.