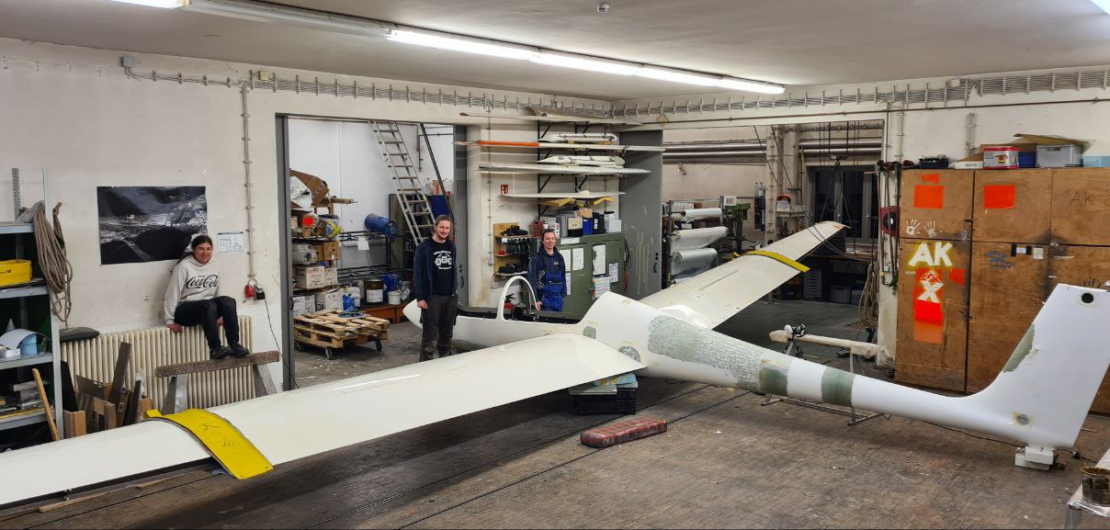
Monatsupdate Dezember
AK-X
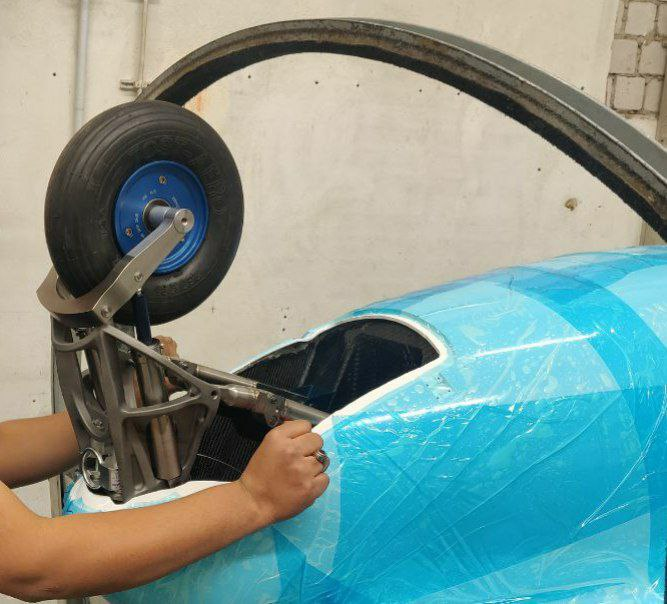
Nach Erhalt der letzten Teile für das Bugfahrwerk stand diesen Monat der Einbau der Fahrwerke in den Rumpf an. Da es sich hier ja um einen Prototypen handelt und wir im vorhinein die Fahrwerkskastenöffnung bewusst zu klein gelassen haben, waren noch einige Anpassungsarbeiten nötig. Diese sind nun alle abgeschlossen. Das Ausfahren mithilfe der Hydraulik wird hier der nächste Schritt sein, mit dem dann die Fahrwerke komplett fertig sind!
Die Schweißteile, die noch in Stuttgart beim Luftfahrtschweißer lagen, wurde abgesehen von den vorderen Knickstreben alle geschweißt. Als nächstes kann man somit das Hauptfahrwerk ebenfalls einbauen. Mit dem fertig geschweißten Steuerknüppel konnte nun die gesamte Hauptsteuerung zusammengeschraubt werden. Lediglich die Frästeile der Mischerplatten werden aktuell noch gefertigt bei einem Unternehmen.
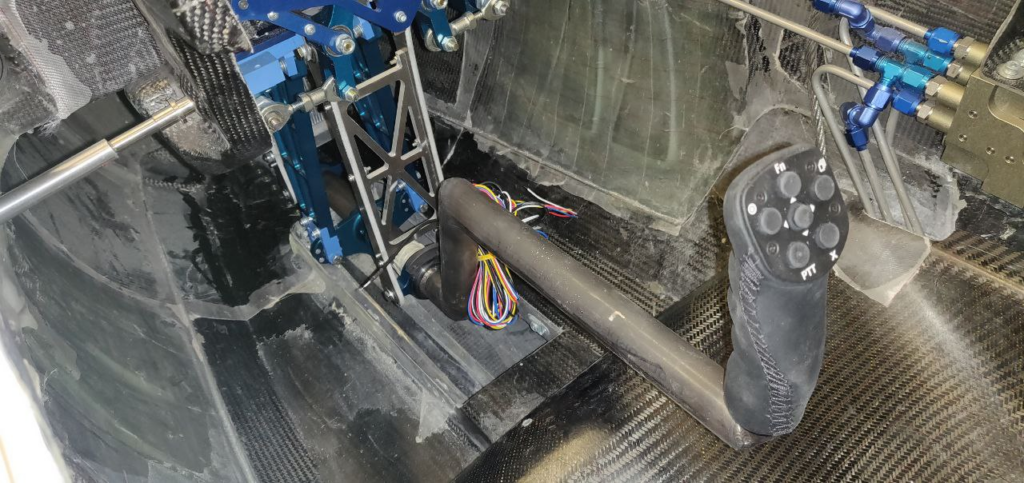
Die Vertiefungen der Ruderunterseiten sind fertig gespachtelt und wir warten hier nun auf die Fertigstellung der Lackierung der Tragflächen. Das zweite Seitenruder mit integrierter Funkantenne wurde gebaut, anschließend wurden beide Teile besäumt. Am Ende des Jahres lässt sich zusammenfassen, dass im Jahr 2024 der Fortschritt an der AK-X wirklich gut war. Jetzt gibt es eigentlich gar nicht mehr so viel zu tun, bis das Flugzeug flugfertig ist!
Twin-Projekt
Im Dezember wurden trotz Winterwartung gute Fortschritte erzielt. Zahlreiche Schäftstellen am Rumpf wurden eingeschliffen und am oberen SR-Scharnier sowie an der Pedalverstellung weitergearbeitet. HLW und HR wurden vermessen und erfolgreich zueinander angepasst. Für die Vermessung der Einstellwinkeldifferenz zwischen HLW und Flächen wurden Lehren gefertigt. Der letzten Monat angekündigte Rohaufbau des Fliegers hat sich als arbeitsintensiv erwiesen, da die Schäftstellen an den rumpfseitigen QK-Buchsen breiter und dicker sind, als die originale Kontur und daher die Flächen durch iterative Steckversuche und Bearbeiten der Flächenschalen per Dremel angepasst werden mussten. Zudem wurden die QK-Rohre ausgebaut, gesäubert und gefettet, um ein einfacheres (wenn auch immer noch schweres) Einstellen dieser zu ermöglichen. Nach Anläufen an drei verschiedenen Tagen, ist es schließlich zum Jahresende am 30.12. gelungen, beide Flächen zu stecken und alle 4 Anschlüsse zu verriegeln. Damit konnten wir 2024 mit einem wichtigen Meilenstein zu beenden!
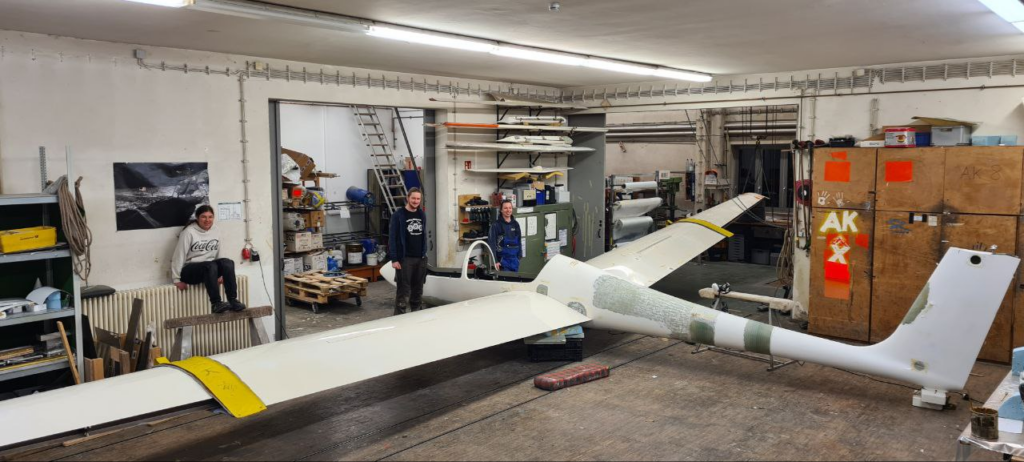