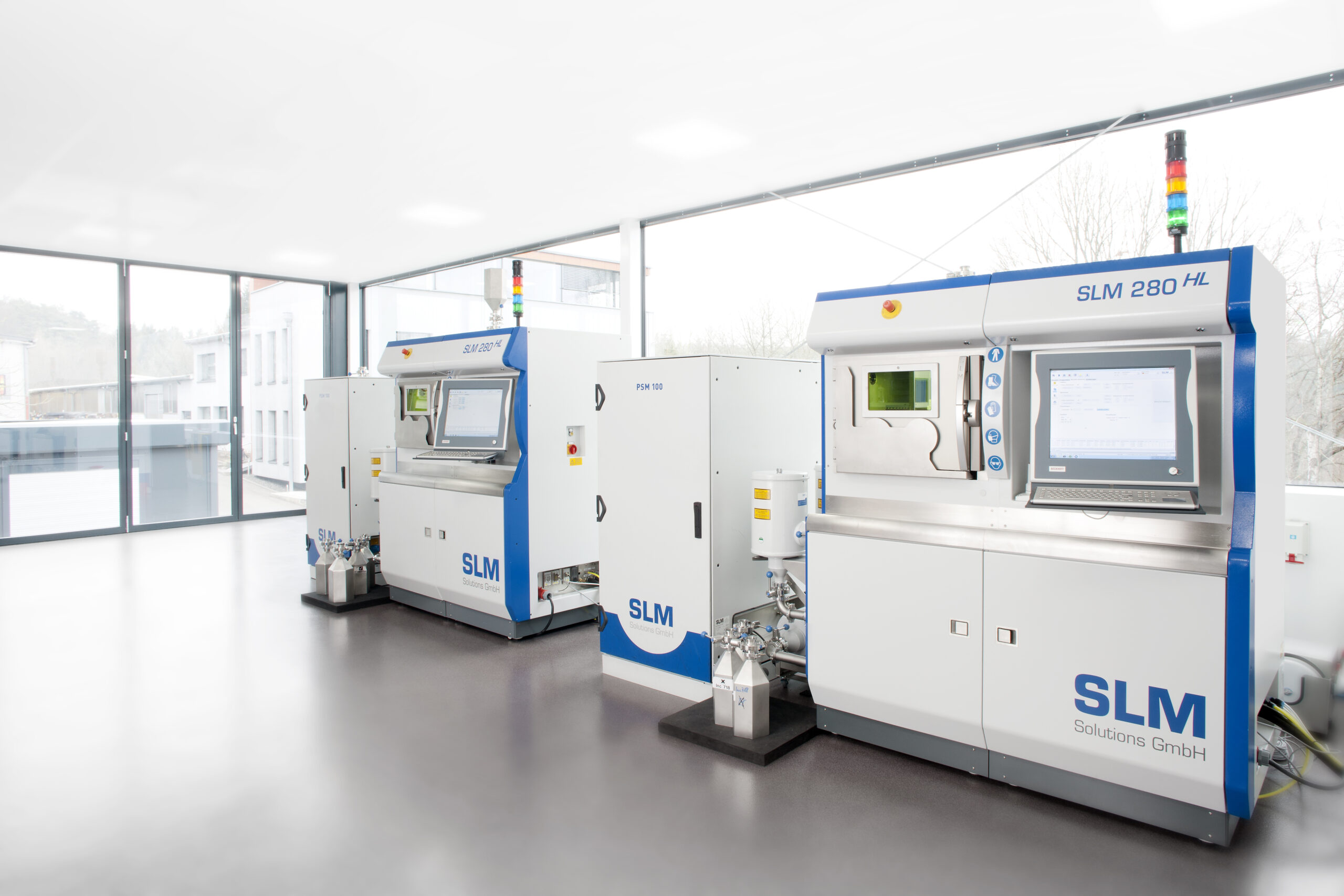
3D-Druck Steuerungsbauteile
3D-Druckverfahren in der Luftfahrt? Letztes Jahr haben wir schon von unserer Anwendung in der Formmanipulation berichtet. Doch „fliegende Teile“ mit einem Drucker fertigen, noch dazu als Teil der Steuerung? Das ist eine Nummer größer, zu groß, dachten auch wir lange. Der Aufwand, so etwas zu entwickeln und zu testen wäre für uns allein finanziell und zeitlich viel zu groß. Wie gut, dass an so etwas auch andere Leute großes Interesse haben, da es von vielen als Schlüsseltechnologie angesehen wird. Im letzten halben Jahr haben wir so eine Kooperation mit der Firma Rosswag und dem IAM-WK am KIT ins Leben gerufen. Nun ist es spruchreif und die ersten Materialproben befinden sich in der chemischen Analyse. Im nächsten Schritt werden dann die mechanischen Probekörper gedruckt. Diese werden dann von einem unserer Mitglieder in den Laboren des IAM getestet und anschließend für das Luftfahrt Bundesamt (LBA) dokumentiert. So streben wir an, Metall-3D-gedruckte Lagerpunkte für Hebel der Steuerung der AK-X fertigen und einsetzen zu dürfen. Der Vorteil solcher Bauteile für uns im Prototypenbau ist die Möglichkeit sehr komplexe Geometrien und Funktionen in einem einzelnen Bauteil realisieren zu können. Das wiederum vereinfacht die übrige Konstruktion sehr stark, was wiederum Zeit und Geld spart, die Montage vereinfacht und Funktionalität sicherstellt. Auch eine Gewichtsersparnis kann erreicht werden, ist jedoch nicht unser primäres Ziel.
Wir sind gespannt wie es weitergeht und hoffen, zusammen mit unseren Partnern die Allgemeine Luftfahrt technologisch voranzubringen.