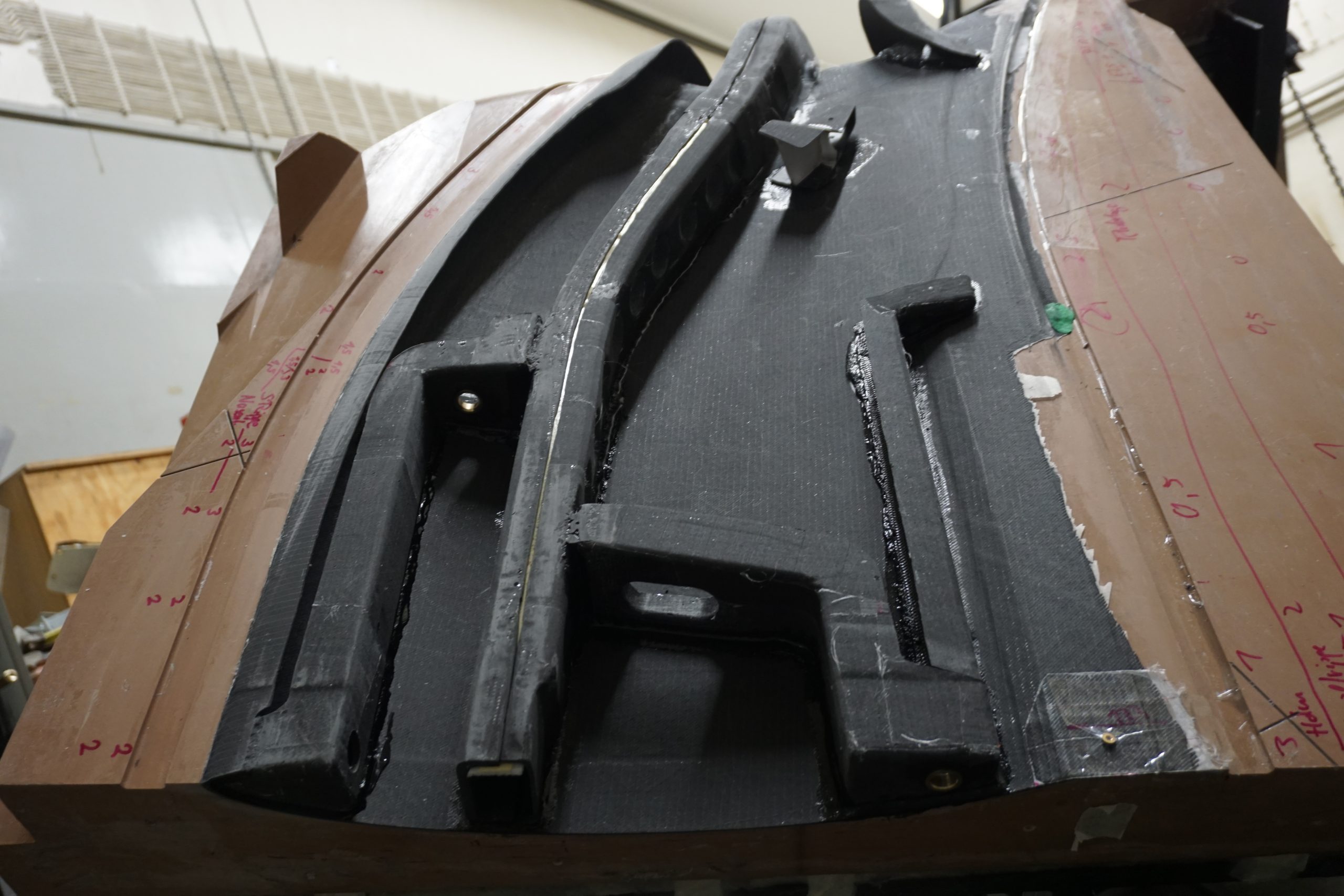
Bruchwinglet – Part III
Wie im letzten Artikel zum Bruchwinglet berichtet, sind die Schalen die größten und bei der AK-X auch aufwändigsten Einzelteile der Winglets. Nach deren Fertigstellung fehlt allerdings noch ein Großteil der Struktur, nämlich Holm- und Endleistenstege zur Kraftübertragung zwischen den Gurten bzw. den Schalen sowie einige Rippen und Stege für die Steckung zwischen Flügel und Winglet und ein Lagerbock für die Steuerung.
Für die passgenaue Fertigung haben wir zwei verschiedene Verfahren gewählt:
Die kleineren Teile, die präzise positionierte Bohrungen für die Steckungsbuchsen oder Lagerungen benötigen, sind geometrisch teils komplex. Wie auch schon für viele andere Einbauteile der AK-X wurden hierfür Formen FDM-3D-gedruckt. Das hat den Vorteil, dass kostengünstig und mit wenig Vorlauf- und Arbeitszeit auch komplizierte Formen realisiert werden können, die geometrisch gut dem CAD-Modell entsprechen.
Für die Holm- und Endleistenstege ist dieses Verfahren jedoch allein durch die größeren Abmessungen unpraktisch. Außerdem kommt es hier weniger auf exakt dem CAD-Modell entsprechende Geometrie an, sondern es ist wichtig, dass die Teile genau in die Schalen und somit zur realen Form der schon hergestellten Struktur passen. Dafür haben wir die Schalen geschlossen und den so entstehenden „Bauraum“ ausgeschäumt. Aus dem entformte Schaumkern wurden Positive, die den späteren Teilen entsprechen, ausgeschnitten und mittels Schleifen und Spachteln der gewünschten Form angepasst. Auf diesen Positiven konnten nun konventionelle GfK-Negativformen laminiert werden. Zur Verstärkung gegen Beulen wurden zugunsten eines niedrigen Bauteilgewichts und einfacher Herstellung Sicken durch in die Form geklebte „Linsen“ modelliert.
Formen sind im Prototypenbau oft die halbe Arbeit, und so konnten wir die eigentlichen Teile in wenigen Laminieraktionen zügig bauen.
Bei den Vorbereitungen zum Einkleben der Teile in die Oberschale zeigte sich der Vorteil des vielschrittigen Formenbaus: Insbesondere die mittels Schaumkern geformten Stege passen perfekt. Zuerst wurden die Stege im senkrechten Teil des Winglets eingeklebt. Für die sechs verbleibenden Teile machte sich die besondere Unterkonstruktion der Formen bezahlt: ohne eine horizontal ausrichtbare Verklebefläche (wenn auch in etwas unergonomischer Höhe) wäre die gleichzeitige genaue Positionierung der einzuklebenden Teile kaum möglich.
Schließlich konnten wir das Bruchwinglet endlich zukleben. Normalerweise ist das der letzte große Arbeitschritt an der Struktur einer Baugruppe. Doch was ist schon normal beim Bau eines Nurflügels? Um eine weitere strukturelle Besonderheit der Winglets und die letzten Arbeiten am Bruchversuchsteil geht es im nächsten Artikel…
Zuerst wurden die Schalen mit Folie ausgekleidet und mit Wachsplatten ein Verklebespalt simuliert. Dann wurde die Form geschlossen und der Hohlraum ausgeschäumt. Aus dem Schaumkern lassen sich Formkerne für die Einbauteile gewinnen… … aus denen wiederum konventionelle Negativformen entstehen. Schließlich werden darin die Holm- und Endleistenstege laminiert. Andere Einbauteile entstehen in 3D-gedruckten Formen. Genaues Ausrichten vor dem Einkleben in die Schale Fertig eingeklebte Teile und Schaumbarrieren für das Verklebeharz Fertig aufgetragenes Verklebeharz kurz vor dem finalen Schließen der Form