Baufortschritt nach dem Einlegen der Rumpfschale im Frühjahr 1996 bis zur Montage des Höhenleitwerks im Sommer 1998
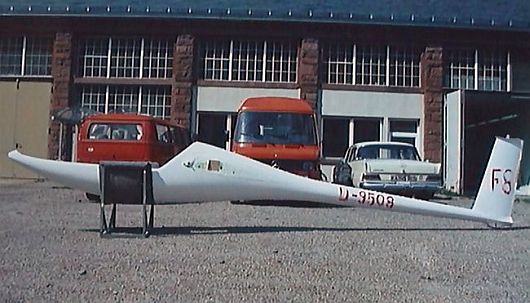
Im April/Mai 1996 wurde der Rumpf der AK-8 in einer Bauaktion bei der Glaser-Dirks Flugzeugbau GmbH (jetzt DG-Flugzeugbau) in den Formen der DG-600 gefertigt. Die Schale hat die Belegung des Motorseglers, so dass wir einen ziemlich leichten Rumpf bekommen haben. In dem Zustand, den das obige Bild zeigt, haben wir ihn dann in unsere Werkstatt geholt. Einige Kleinigkeiten (wie die Lackierung und das Finish der Klebenähte) sind seitdem noch gemacht worden.
Da wir die Steuerung im Rumpf noch nicht auf die AK-8 angepasst haben, fehlen noch einige Einbauten (wie der Fahrwerkskasten). Die Konstruktion dieser Teile, der Flügelsteuerung, der Nachweis des Rumpfes (im Rahmen der Studienarbeit von Christoph Lenz) beschäftigen uns im Moment.
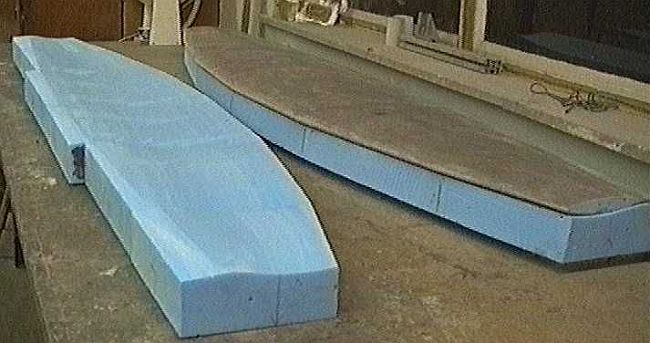
Ende November/Anfang Dezember wurde bei DG-Flugzeugbau der Haubenrahmen der AK-8 gebaut. Obwohl der Haubenrohling schon von Mecaplex geliefert wurde ist er noch nicht mit dem Rahmen verklebt worden, da der Rumpf (und mit ihm der Haubenrahmen) noch einmal mit den fehlenden Einbauten getempert werden muss. Dies ist mit bereits aufgeklebtem Haubenglas nicht möglich.
Zudem wird gerade am Urpositiv des Höhenleitwerks gebaut, welches man oben noch im „rohen“ Zustand sieht. Gezeigt ist der GFK-umhüllte Kern (rechts) ohne aufgetragenen Lack, dafür aber mit dem ROOFMATE-Block, (links und unter dem Kern) aus dem er mit dem Hitzdraht ausgeschnitten wurde. Auch der Anschluss des Höhenleitwerks und des Höhenruders an den Rumpf ist im Bau.
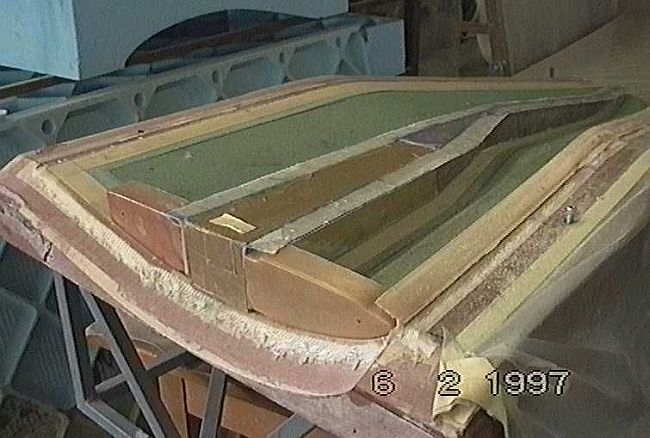
Mittlerweile ist es Februar und das Urpositiv des Höhenleitwerks ist fertiggestellt. Direkt im Anschluss wird mit dem Bau der Höhenleitwerksform begonnen.
Auch der Ansteckflügel, von dem zunächst einmal ein Teststück in Glasfaser gebaut wird, nähert sich langsam seiner Fertigstellung. Zusätzlich wird gerade am Seitenruder, dem Höhenleitwerk/Höhenruder und der Steuerung gebaut und konstruiert. Auch weitere Aluminiumsegmente der Tragflügelformen treffen jetzt immer wieder in der Werkstatt ein.
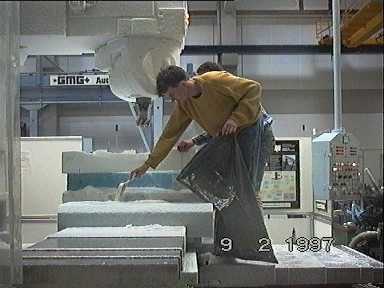
Die letzten Schaumsegmente sind gefräst. Auf Wunsch der Gießerei haben wir dabei von Roofmate auf Styropor umgestellt, welches sich direkt vergießen lässt. Wie man auf den Bilder sehen kann, verwandelte sich bei der Bearbeitung die Bokö langsam in eine Winterlandschaft. Insgesamt waren es hinterher ein Dutzend blaue Müllsäcke voll mit Styropor. Inzwischen sind von der Gießerei mehr als die Hälfte der Aluminiumsegmente gegossen worden, da jedoch leider der Antriebsmotor der Fräsmaschine zur Zeit defekt ist, ist davon bisher nur die Hälfte, das heißt insgesamt ein viertel – oder eine komplette Form – fertiggestellt.
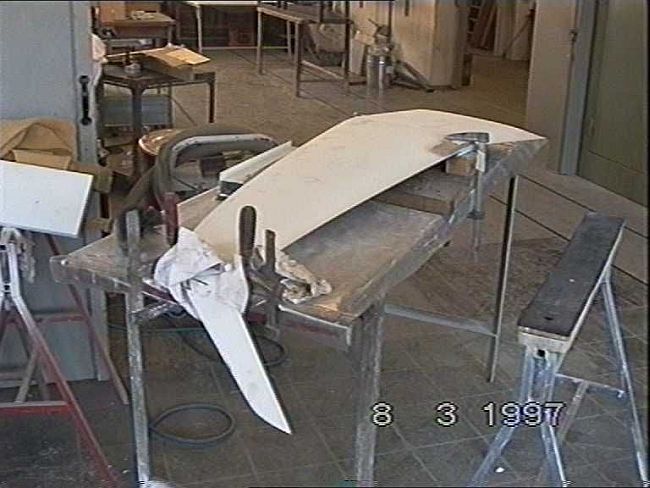
Auch die Höhenleitwerksform macht Fortschritte. Die Unterseite ist fertiggestellt, aufgrund eines Missgeschicks beim Entformen der Klebeleiste musste jedoch die Formoberseite noch einmal nachlackiert werden. Seit Freitag (21.3.) ist jedoch alles zum Abformen der zweiten Formhälfte vorbereitet.
Das Musterstück des Außenflügels ist geschliffen und gefüllert worden. Nach nochmaligem Überlackieren sah es recht gut aus und diente uns auf der Aero’97 in Friedrichshafen als Ausstellungsstück. Nur gut, dass es kein Besucher des Idaflieg-Standes dort hochheben musste.
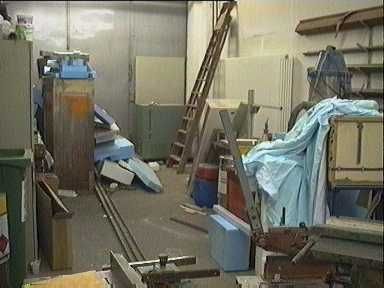
Die Formen des Höhenleitwerks sind mittlerweile fertig, auch die Wurzelrippen der (fliegenden) Ansteckflügel sind gebaut worden. Als weiteres Einbauteil sieht man oben die beiden Bremsklappenkästen, die in den letzten Wochen laminiert wurden und in denen bereits die Hebel und Bleche montiert sind.
Im Moment tut sich in der Werkstatt leider recht wenig, denn die Akaflieg hat schon seit einigen Wochen die Handwerker im Haus, die die gesamten Heizkörper austauschen und den Dachboden isolieren — und dafür sorgen, das jede Ecke in der Werkstatt mit irgendwelchem Gerät zugestellt ist. Da sieht es dann so aus wie auf dem rechten Bild. Wobei das schon nicht mehr den schlimmsten Zustand zeigt.
Aber schließlich war das überstanden und es ging mit dem Bau der Außenflügel weiter:
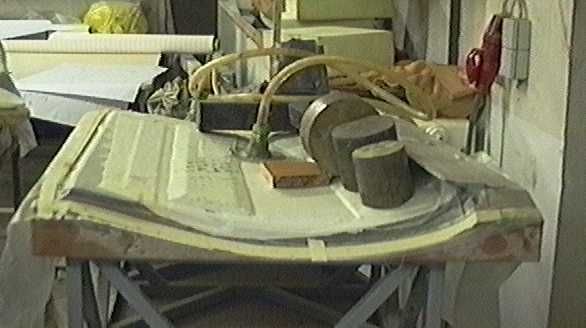
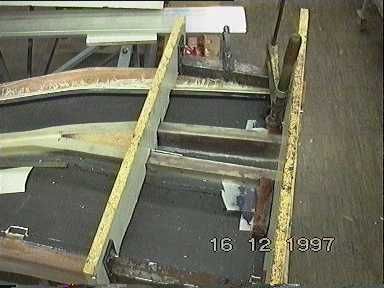
Die Bilder oben zeigen den Bau der 1,5m langen Ansteckflügel der AK-8 vom Einlegen des Außenlaminates mit dem Stützschaum bis zum Einkleben der Einbauten und der Wurzelrippen. Die Flügelschalen sind fertig, die Holmgurte konnten freundlicherweise bei DG-Flugzeugbau gezogen werden, wie die Stege aufgebaut wurden zeigt das Bild unten links. Im rechten Außenflügel sind die Wurzelrippen mit den in ihnen befestigten Querkraftbuchsen, sowie die Buchse für den Holmstummelbolzen mit Hilfe einer Vorrichtung eingeklebt, der linke Flügel ist soweit vorbereitet, das dies als nächstes erfolgen kann. Sobald die Ruderlager für das Außenquerruder gesetzt sind können beide Außenflügel verklebt werden. Das kommt jedoch erst im neuen Jahr.
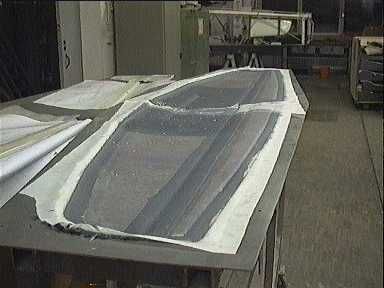
Zu Anfang des Jahres konnten beide Außenflügel verklebt, entformt und getempert werden. Das Aussägen der Querruder hat bis jetzt noch nicht stattgefunden und auch beschäumt sind die beiden Flügel noch nicht. Die Lager des Ruders und den hinteren Querkraftbolzen kann man auf der Detailaufnahme sehr gut erkennen.
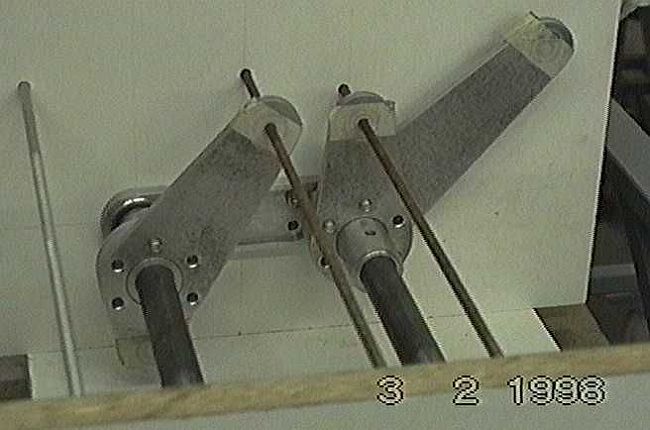
Nachdem die Formen der Außenflügel weggeräumt werden konnten, wurde an der Querruder- und Bremsklappen-Steuerung im Rumpf gearbeitet. Die Bilder oben zeigen einen Blick in den Rumpf mit den beiden Lagerböcken der Antriebswellen und dann eine Probemontage der beiden Lager, beider Wellen und der auf ihnen befestigten An- und Abtriebshebel.
Parallel dazu begann der Bau des Höhenleitwerks, von dem einzelne Einbauteile schon im vergangenen Jahr gefertigt wurden. Zunächst ist die Oberschale des Leitwerks mit Außenlaminat, Stützschaum und Innenlaminat eingelegt worden, anschließend folgte das Außenlaminat der Unterschale. Die Schäume fehlen hier noch, da vorher die Verriegelung des Leitwerks am Rumpf eingebaut werden muss.
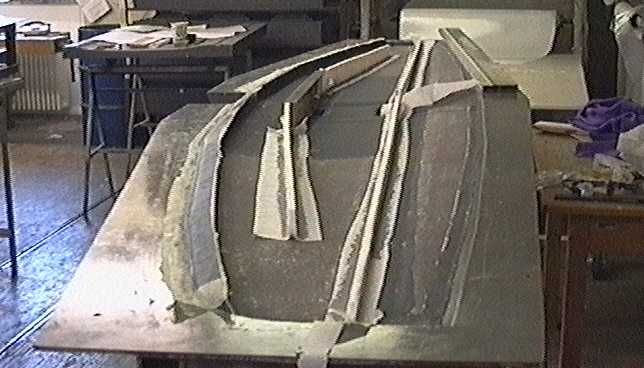
Schäume, Innenlaminat und der T-Beschlag für den Anschluss des Leitwerkes an den Rumpf sind in die Unterschale des Höhenleitwerks eingebaut. Auch die Verriegelung (ganz vorn in der Flügelnase) ist bereits eingeklebt. Der Hauptsteg und der Abschlusssteg, wobei in letzteren noch die Ruderlager eingebaut werden müssen, sind ebenfalls vorhanden, allerdings noch nicht belegt.
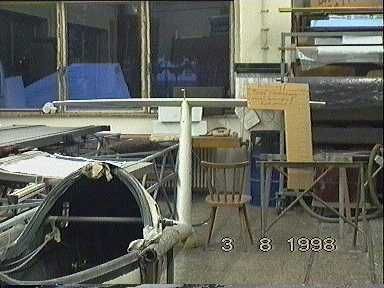
Das Höhenleitwerk ist entformt und bereits an den Rumpf angepasst, wie man den obigen Bildern entnehmen kann. Absägen des Ruders, Anformen einer Rudernase und Verputzen der Leitwerksnase sind die Schritte, die bis zur Fertigstellung noch fehlen, während die Lackoberfläche schon sehr gut aus der Form gekommen ist, wie man an den Spiegelungen in der Oberfläche sehen kann.
Der Flügel-Rumpf-Übergang der AK-8 liegt mittlerweile auch im wesentlichen fest, so dass auch die Holmstummelformen in Schaum gefräst werden konnten. Die sind mittlerweile bei der Gießerei MGM in Mannheim und nach deren Rückkehr als Alurohlinge kann die Flügelform komplettiert werden.
Am Höhenleitwerk ist das Ruder abgetrennt, die Rudernase angeformt und verputzt worden, die Anlenkung Rumpfseitig ist endgültig eingebaut, die Höhensteuerung somit funktionsfähig.
Lediglich das Finish fehlt dem Leitwerk noch. Das Seitenruder ist mittlerweile angepasst und gängig, auch an diesem Bauteil fehlt nur noch das endgültige Finish.
Bei den Flügelformen der AK-8 sind alle großen Aluminiumssegmente fertig gefräst, die meisten auch bereits bei AHC-Oberflächentechnik mit einer Verschleißschutzschicht beschichtet worden.
Die letzten Teile sind gegossen und können in der kommenden Woche bei der Gießerei abgeholt werden. Bis Ende Januar dürften die Formen somit komplettiert sein. Zur Zeit werden die Segmente angepasst und noch einige Befestigungspunkte angeschweißt, wie die Bilder zeigen.
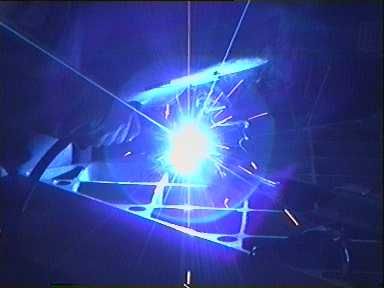