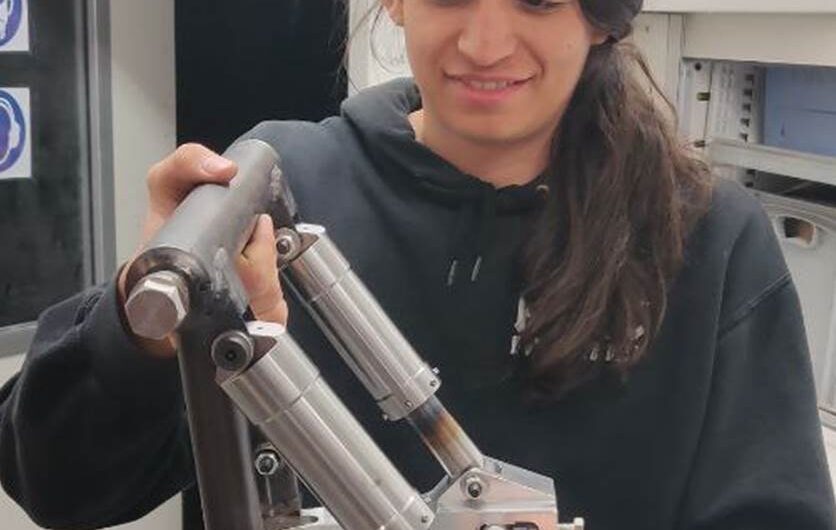
Monatsupdate Oktober
Diesen Monat ging es wieder an vielen Stellen bei der AK-X weiter:
Zum Einen wurden viele Teile fertiggestellt und zum Luftfahrtschweißer der Akaflieg Stuttgart gebracht. Hierzu zählt der Steuerknüppel, die Bedienstange der Bremsklappe, der Verrieglungshacken des vorderen Fahrwerkes, die Lagerung der Seitenruderanschlusstüte zwischen Winglet und Flügel und die beiden Knickstreben des Hauptfahrwerks. Bei der Gelegenheit konnte auch das geschweißte Fahrwerksbein des Hauptfahrwerks abgeholt werden. Nach Zusammenbau der Dämpfer konnte somit die Baugruppe von Dämpfer, Fahrwerksbein, Schwinge und Achse das erste Mal zusammengebaut werden (siehe Bild).
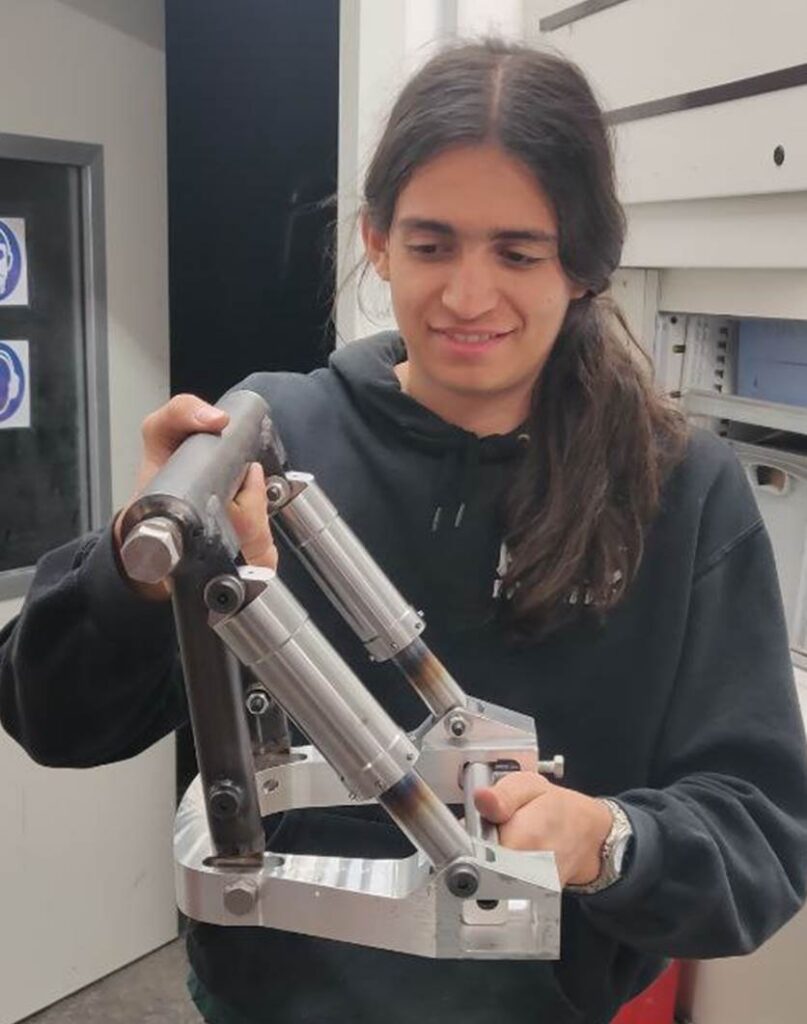
Die letzten Titanfrästeile der Knickstreben des vorderen Fahrwerkes wurden vom ISTM gefertigt, die zugehörigen Schweißgestelle konnten gebaut und die Teile ebenfalls bei Wolf Hirth abgegeben werden. Da die Konstruktion der vorderen Knickstreben jetzt nur noch Rohre sind und die Verbindungsstrebe als Frästeil ausgeführt wird, sind wir zuversichtlich, dass Wolf Hirth diese Schweißen kann.
Parallel hierzu wurde die zweite Dämpferschale des vorderen Fahrwerkes gedreht und gefräst.
Ein weiterer großer Schritt war ebenfalls die Lieferung unserer 3D-gedruckten Bugfahrwerksgabel (siehe Bild). Nach kleinen Anpassungen passt die Bugkupplung hinein und wir hoffen, dass bis zur nächsten Monatsmail das vordere Fahrwerk ähnlich weit wie das Hauptfahrwerk fortgeschritten ist.
Bei der Steuerung wurden alle noch fehlenden Frästeile auskonstruiert und Fertigern zugeschickt, welche bis Ende nächsten Monats gefertigt sein sollten.
Bei den Instrumenten haben wir nun die Komponenten von LXNav erhalten. Hierzu zählt ein LX9000 mit V8 und Hawk, sowie Knüppelfernbedienung und zusätzlichen kleineren Komponenten. Auch hier möchten wir uns ausdrücklich für diese großzügige Unterstützung durch LXNav bedanken!
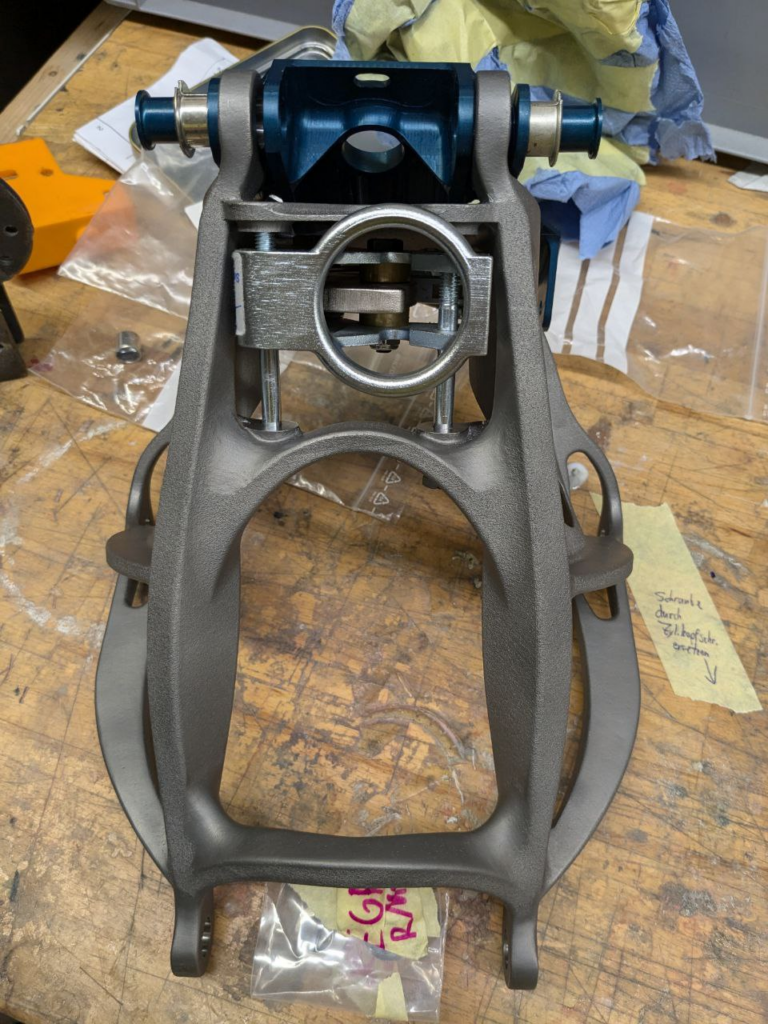
Da der bereits gebaute I-Pilz aus Kohlefaser nicht passt, wurde der I-Pilz angepasst und per 3D-Druck direkt die Negativform gedruckt.
Der Bau aus Glasfaser und das Entformen hat sehr gut geklappt und nächste Woche werden die Ausschnitte auf der Fräse der Akaflieg Stuttgart gefertigt.
Das Gesamtrettungssystem befindet sich aktuell bereits auf dem Weg zu unserer Werkstatt.
Der Schaltplan für die Elektronik wurde erstellt und die Position der Sicherungen, Hauptschalter und Steckern festgelegt.
Bei der Lackierung der AK-X ging es nun endlich voran, seitdem ein Mitarbeiter nach längerem Krankheitsausfall nun daran arbeitet. Davor haben wir noch einige Anpassungsarbeiten am Rumpf gemacht, damit die Lackierung schneller voran geht. Wir hoffen, dass der Rumpf bis Mitte November fertiggestellt ist, sodass man hier die restlichen Baugruppen einpassen kann.
Es geht mit großen Schritten voran, was aber auch nötig ist, damit der Standschwingversuch Anfang nächsten Jahres durchgeführt werden kann.