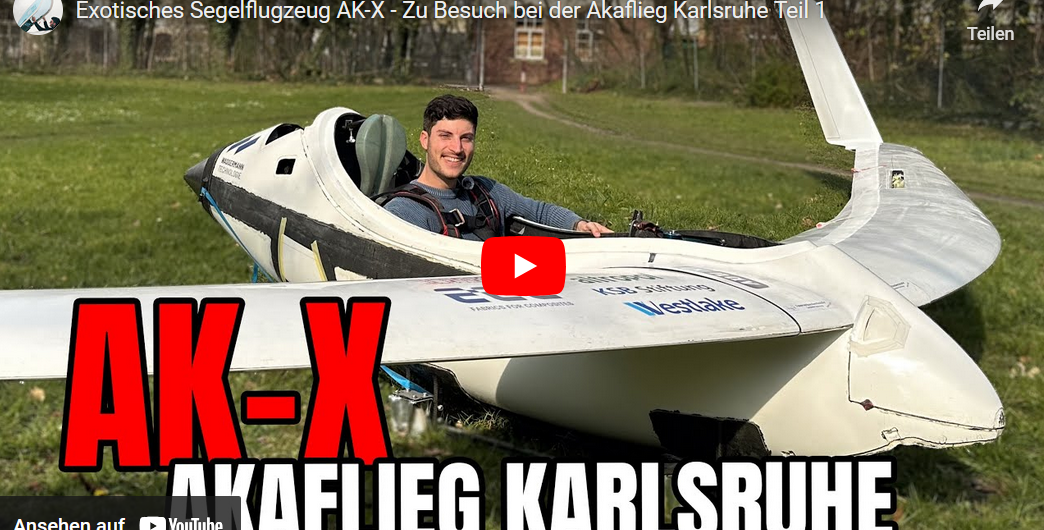
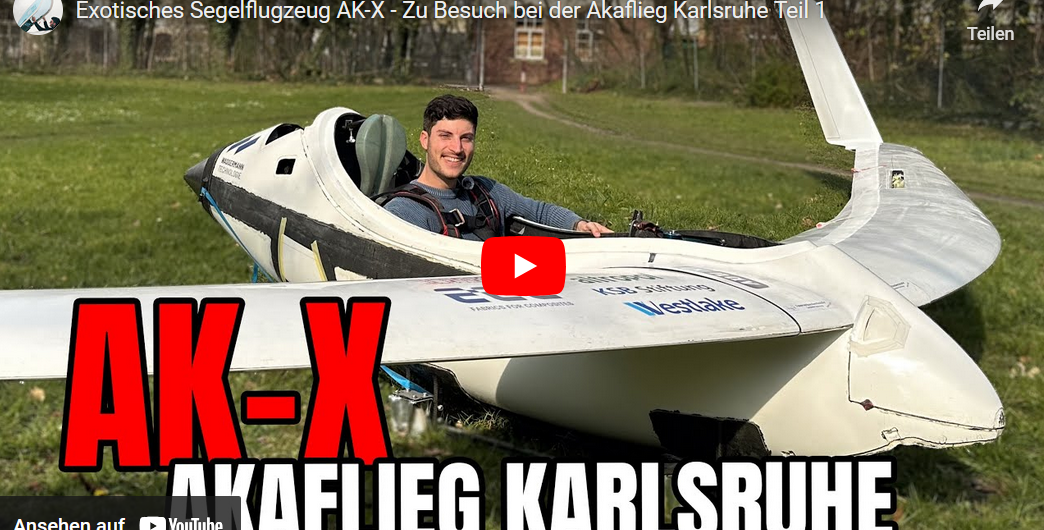
Nach Erhalt der letzten Teile für das Bugfahrwerk stand diesen Monat der Einbau der Fahrwerke in den Rumpf an. Da es sich hier ja um einen Prototypen handelt und wir im vorhinein die Fahrwerkskastenöffnung bewusst zu klein gelassen haben, waren noch einige Anpassungsarbeiten nötig. Diese sind nun alle abgeschlossen. Das Ausfahren mithilfe der Hydraulik wird hier der nächste Schritt sein, mit dem dann die Fahrwerke komplett fertig sind!
Die Schweißteile, die noch in Stuttgart beim Luftfahrtschweißer lagen, wurde abgesehen von den vorderen Knickstreben alle geschweißt. Als nächstes kann man somit das Hauptfahrwerk ebenfalls einbauen. Mit dem fertig geschweißten Steuerknüppel konnte nun die gesamte Hauptsteuerung zusammengeschraubt werden. Lediglich die Frästeile der Mischerplatten werden aktuell noch gefertigt bei einem Unternehmen.
Die Vertiefungen der Ruderunterseiten sind fertig gespachtelt und wir warten hier nun auf die Fertigstellung der Lackierung der Tragflächen. Das zweite Seitenruder mit integrierter Funkantenne wurde gebaut, anschließend wurden beide Teile besäumt. Am Ende des Jahres lässt sich zusammenfassen, dass im Jahr 2024 der Fortschritt an der AK-X wirklich gut war. Jetzt gibt es eigentlich gar nicht mehr so viel zu tun, bis das Flugzeug flugfertig ist!
Im Dezember wurden trotz Winterwartung gute Fortschritte erzielt. Zahlreiche Schäftstellen am Rumpf wurden eingeschliffen und am oberen SR-Scharnier sowie an der Pedalverstellung weitergearbeitet. HLW und HR wurden vermessen und erfolgreich zueinander angepasst. Für die Vermessung der Einstellwinkeldifferenz zwischen HLW und Flächen wurden Lehren gefertigt. Der letzten Monat angekündigte Rohaufbau des Fliegers hat sich als arbeitsintensiv erwiesen, da die Schäftstellen an den rumpfseitigen QK-Buchsen breiter und dicker sind, als die originale Kontur und daher die Flächen durch iterative Steckversuche und Bearbeiten der Flächenschalen per Dremel angepasst werden mussten. Zudem wurden die QK-Rohre ausgebaut, gesäubert und gefettet, um ein einfacheres (wenn auch immer noch schweres) Einstellen dieser zu ermöglichen. Nach Anläufen an drei verschiedenen Tagen, ist es schließlich zum Jahresende am 30.12. gelungen, beide Flächen zu stecken und alle 4 Anschlüsse zu verriegeln. Damit konnten wir 2024 mit einem wichtigen Meilenstein zu beenden!
Diesen Monat ging es wieder an vielen Stellen bei der AK-X weiter:
Zum Einen wurden viele Teile fertiggestellt und zum Luftfahrtschweißer der Akaflieg Stuttgart gebracht. Hierzu zählt der Steuerknüppel, die Bedienstange der Bremsklappe, der Verrieglungshacken des vorderen Fahrwerkes, die Lagerung der Seitenruderanschlusstüte zwischen Winglet und Flügel und die beiden Knickstreben des Hauptfahrwerks. Bei der Gelegenheit konnte auch das geschweißte Fahrwerksbein des Hauptfahrwerks abgeholt werden. Nach Zusammenbau der Dämpfer konnte somit die Baugruppe von Dämpfer, Fahrwerksbein, Schwinge und Achse das erste Mal zusammengebaut werden (siehe Bild).
Die letzten Titanfrästeile der Knickstreben des vorderen Fahrwerkes wurden vom ISTM gefertigt, die zugehörigen Schweißgestelle konnten gebaut und die Teile ebenfalls bei Wolf Hirth abgegeben werden. Da die Konstruktion der vorderen Knickstreben jetzt nur noch Rohre sind und die Verbindungsstrebe als Frästeil ausgeführt wird, sind wir zuversichtlich, dass Wolf Hirth diese Schweißen kann.
Parallel hierzu wurde die zweite Dämpferschale des vorderen Fahrwerkes gedreht und gefräst.
Ein weiterer großer Schritt war ebenfalls die Lieferung unserer 3D-gedruckten Bugfahrwerksgabel (siehe Bild). Nach kleinen Anpassungen passt die Bugkupplung hinein und wir hoffen, dass bis zur nächsten Monatsmail das vordere Fahrwerk ähnlich weit wie das Hauptfahrwerk fortgeschritten ist.
Bei der Steuerung wurden alle noch fehlenden Frästeile auskonstruiert und Fertigern zugeschickt, welche bis Ende nächsten Monats gefertigt sein sollten.
Bei den Instrumenten haben wir nun die Komponenten von LXNav erhalten. Hierzu zählt ein LX9000 mit V8 und Hawk, sowie Knüppelfernbedienung und zusätzlichen kleineren Komponenten. Auch hier möchten wir uns ausdrücklich für diese großzügige Unterstützung durch LXNav bedanken!
Da der bereits gebaute I-Pilz aus Kohlefaser nicht passt, wurde der I-Pilz angepasst und per 3D-Druck direkt die Negativform gedruckt.
Der Bau aus Glasfaser und das Entformen hat sehr gut geklappt und nächste Woche werden die Ausschnitte auf der Fräse der Akaflieg Stuttgart gefertigt.
Das Gesamtrettungssystem befindet sich aktuell bereits auf dem Weg zu unserer Werkstatt.
Der Schaltplan für die Elektronik wurde erstellt und die Position der Sicherungen, Hauptschalter und Steckern festgelegt.
Bei der Lackierung der AK-X ging es nun endlich voran, seitdem ein Mitarbeiter nach längerem Krankheitsausfall nun daran arbeitet. Davor haben wir noch einige Anpassungsarbeiten am Rumpf gemacht, damit die Lackierung schneller voran geht. Wir hoffen, dass der Rumpf bis Mitte November fertiggestellt ist, sodass man hier die restlichen Baugruppen einpassen kann.
Es geht mit großen Schritten voran, was aber auch nötig ist, damit der Standschwingversuch Anfang nächsten Jahres durchgeführt werden kann.
Da wir uns aktuell sehr auf den Projektfortschritt der AK-X fokussieren, kommen wir kaum dazu, wie in der Vergangenheit aufwändige YouTube-Videos zu drehen. Um euch auf trotzdem auf dem Laufenden zu halten, wird es von nun an mindestens ein Mal im Monat einen neuen Blogeintrag zu lesen geben. Vorbeischauen lohnt sich also, viel Spaß!
AK-X
Diesen Monat stand der Rumpfbelastungsversuch im Fokus. Davor mussten noch einige Arbeiten am und im Rumpf erledigt werden. Ein Problem fürs Finish war, dass die (absichtlich weich konstruierte) Rumpschale am Flächen-Rumpf-Übergang bei gesteckten Flügeln um einige Millimeter ausbeulte im Vergleich zum ungesteckten Zustand. Dies konnten wir nach längerer Suche darauf zurückführen, dass der Abstand der Querkraftbuchsen im Rumpf minimal größer war als der Abstand der Bolzen im Flügel und somit die Querkraftholme dort beim Stecken zueinander gezogen wurden. Die Lösung war ein Einschlitzen der Rumpfschale an der entsprechenden Stelle und Zuschäften im gesteckten Zustand. Außerdem wurde der Ausschnitt im „Biertisch“ (Horizontalspant) etwas vergrößert, um mehr Platz für die Hauptsteuerung zu schaffen. Die Lagerbrücke für die Bremsklappensteuerung haben wir dann ebenfalls eingepasst, um die erforderlichen Befestigungslöcher noch vor dem Belastungsversuch zu bohren.
Parallel haben wir ein Belastungsgestell gebaut, das leicht modifiziert auch Versuche am Flügel zulässt, sollten diese später noch nötig sein. Nach Tempern, Ausleihen von Zink- und Stahlgewichten und dem Kauf einer Tonne Estrich war es dann soweit und wir konnten den Rumpf mit Gewicht vollschaufeln. Zum Erreichen der für 6,6 g Last erforderlichen ca. 1,9t Material mussten wir außerdem Paletten mit Gewichten unten an den Rumpf hängen. Leider hat sich beim eigentlichen Versuch das Belastungsgestell an der Einspannung des Rumpfes deutlich stärker verformt als erwartet. Dadurch mussten wir den Versuch abbrechen und das Gestell konstruktiv anpassen. Wir sind aber zuversichtlich, den Versuch mit den eingeflossenen Verbesserungen bald wiederholen zu können.
Am Flügel ging es an den Details weiter. Wir haben den Flügel für den Einbau der Wasserballastventile vorbereitet und deren Stecker in die Wurzelrippe eingebaut. An den Bremsklappen wurden letzte Kollisionen beseitigt und die Verriegelungskräfte eingestellt. Außerdem wurden die Ruderscharniere, Öffnungen für die Anlenkung und Abdichtungsplatten der Anlenkung final besäumt bzw. eingepasst. Schließlich haben wir Profilschablonen zum genauen Einschleifen der Oberflächenkontur von Flügel und Winglet konstruiert und deren Fertigung begonnen.
Die Winglets wurden beide im Vertikalteil final besäumt und Abdeckungen für Bolzen und Seitenruderanschluss konstruiert; das erste Paar davon ist schon laminiert. Außerdem konnte der Lagerbock der Ruderanschlusstüte gefräst werden und die Bleche des entsprechenden Gegenstücks wurden wasserstrahlgeschnitten, zusammen mit einigen weiteren Steuerungsteilen für den Rumpf.
Die Haube war noch einmal beim Hersteller, um das Haubenfenster einzupassen. Bei uns wurden die Scharniere und der Verriegelungsmechanismus finalisiert, sodass bis auf rumpfseitigen Notabwurfmechanismus, Verriegelungsseil und Lackierung alles fertig ist.
Die Platine für die Trimmung wurde gelötet und der Microkontroller erfolgreich auf Funktion überprüft. Die LED-Platine des ACL im Bug wurde gelötet, die damit kombinierte Staurohraufnahme gefräst und alles in transparentem Harz vergossen.
Für die Lüftung haben wir neue Lufteinlässe laminiert und eine Abdichtung des Bugfahrwerkskastens konstruiert und gebaut. Außerdem haben wir die Bugfahrwerksklappen laminiert, eingepasst und mit ihren Scharnieren verklebt.
Das Sondermessprojekt „Digital Zachering“ der Akaflieg Karlsruhe hat die Grundidee, den Flugzustand eines Segelflugzeuges möglichst gut mit einfachen Mitteln abzubilden. Die ersten Messflüge konnten Anfang August auf dem Sommertreffen der idaflieg durchgeführt werden.
Das Sommertreffen wird von der idaflieg (Interessengemeinschaft Deutscher Akademischer Fliegergruppen) organisiert. Besondere Unterstützung kommt dabei vom Deutschen Zentrum für Luft-und Raumfahrt (DLR) und dem Luftfahrtbundesamt (LBA).
Beim Sommertreffen kommen Mitglieder aller deutschen Akafliegs für drei Wochen zusammen, um das wissenschaftliche Fliegen zu üben und diverse Sondermessprojekte (SMPs) durchzuführen. Diese Sondermessprojekte können Erprobungsflüge von Prototypen oder aber ganz andere Forschungsprojekte, wie eben das Digital Zachering, sein. Das Großartige ist, dass man sich bei der Veranstaltung mit vielen Experten aus ganz Deutschland austauschen kann. Zudem werden die Kosten für die Messflüge vom DLR übernommen.
Das Zachern ist einer der Hauptschwerpunkte des Sommertreffens. Es dient der systematischen Erfassung der Flugeigenschaften eines Flugzeuges und gleichzeitig der Ausbildung von Piloten im Bereich des wissenschaftlichen Fliegens. Dabei müssen die Piloten diverse Steuereingaben geben und beobachten wie sich das Flugzeug verhält. Die erfassten Daten werden auf Papier festgehalten. Mit dem Digital Zachering wird zusätzlich zu der handschriftlich erfassten Beobachtung eine digitale Aufnahme der Flugbewegung realisiert.
Als Herzstück des Messsystems dient ein Pixhawk Autopilot für unbemannte Luftfahrsysteme (UAS). Die Cube- und Ardupilot-Projekte sind dabei für uns besonders interessant, da sie Open-Source sind. Es können also alle Hardware- und Softwarekomponenten nachvollzogen werden und eigene Weiterentwicklungen sind dank guter Dokumentation für viele Studenten realisierbar. Mit dem CubePilot ist es uns möglich, zuverlässig umfangreiche Datensätze zu generieren. Er verfügt sowohl über ein internes Sensorsystem zum Flugzustand und bietet darüber hinaus viele Schnittstellen für externe Messtechnik. Neben des GPS- und lagebasieren Navigationssystems haben wir für Erfassung der Strömung und des Flugzustanden in dieser Kampagne ein einfaches Prandtl-Rohr, sowie einen Temperatur- und Feuchtesensor verwendet.
Eine weitere Herausforderung war das aerodynamische Gehäuse der Box. Diese wurde am Institut für Mikroverfahrenstechnik am KIT aus SLA-Harz gedruckt. An diesem Institut konnten wir auch schon OpenAccess 5-Lochsonden (The Oxford Probe), mittels BinderJetting, additiv fertigen. Eine Oxford-Sonde soll im Winter in das Messsystem integriert werden. Das spannende an diesen Sonden ist, dass sie nicht im Windkanal kalibriert werden müssen (Hall and Povey 2017). Wir wollen diese Sonden erstmals für die Flugdatenerfassung einsetzen.
Einige Wochen vor Beginn unserer Messkampagne auf dem idaflieg-Sommertreffen haben wir tatkräftige neue Teammitglieder aus der Akaflieg Braunschweig gewonnen. Die Akaflieg Braunschweig arbeitet ebenfalls an Konzepten zur Flugdatenerfassung und -auswertung. Unverhofft kommt oft und so führen wir das Projekt jetzt überregional durch, ganz im Sinne der idaflieg. In Brauschweig wurde ein Online-Tool, speziell für die Auswertung der Messpoddaten entwickelt. Hiermit können Piloten ihre Flugdaten interaktiv mit einer Python-basierten Web-App auswerten. Es geht insbesondere darum einzelne Flugmanöver schnell und einfach in den Daten zu markieren und mit zusätzlichen Metadaten zu versehen. Dabei sind interessante Punkte zum Beispiel die erflogenen Manöver, in welcher Flugzeugkonfiguration gestartet wurde oder besonderheiten des Wettergeschehens. Mit diesen Metadaten wird die Auswertung der Manöver in Nachgang wesentlich vereinfacht, vor allem wenn längere Zeit zwischen dem Flug und der Auswertung liegt. Die Web-App ist auch eine hervorragende Möglichkeit für Piloten, den eigenen Flug und die Erfahrung unter Einbezug von echten Messdaten zu rekapitulieren.
Schon im letzten Jahr haben wir eine – damals noch kastenförmige – Messbox entwickelt. Die Sensoren, im Speziellen Fünflochsonde, Inertia Navigation System, Druck-, Feuchte – und Temperatursensoren wurden von der Arbeitsgruppe Umweltphysik an der Uni Tübingen bereitgestellt. 2020 konnten einige Unklarheiten bei der Zulassung nicht ausgeräumt werden. Daher haben wir uns entschlossen für das Jahr 2021 einige grundsätzliche Änderungen im Design, wie oben beschrieben, umzusetzen.
Durch diese Erfahrung war bereits im Vorfeld klar, welche Punkte wir bei der Zulassung beachten müssen. Dies ist auch für die Gruppe eine gute Möglichkeit gewesen, um sich an der Zulassung von (Mess-)Anbauten zu versuchen. Insbesondere haben wir ganz am Anfang, gemeinsam mit Werner „Micro“ Scholz von der SFL GmbH, eine Liste von möglichen Szenarien entworfen, die sicherheitsrelevant sind und daher gleich in der frühen Konzeption für die Zulassung berücksichtigt werden müssen. Für uns war besonders die Festigkeit beim Crashfall entscheidend. Hierbei musste nachgewiesen werden, dass der gesamte Verbund auch im Crashfall am Leitwerk haften bleibt und somit auch nicht ins Cockpit einschlägt. Durch die Rechnungen konnten wir nachvollziehen dass der Verband sehr sicher am Leitwerk haftet. Einen anderen, wichtigen Punkt stellte die Lage des Schwerpunktes und der sich daraus verändernde Trimmplan dar. Bei Interesse kann gerne auf das gesamte Know-How der Zulassung zurückgegriffen werden. (Anfragen an: messpod@akaflieg-karlsruhe.de)
Zur Dokumentation gibt es einen Gitlab Repository, auf welchen jede interessierte Person Zugriff bekommen kann. Zudem sind die Gesichtspunkte der Zulassung auf dem idaflieg-Server hinterlegt. Bei weiteren Fragen kann man sich gerne jeder Zeit an die Akademische Fliegergruppe Karlsruhe wenden.
Nach vielen Monaten der Vorbereitung ging es auf das Sommertreffen. Hier konnten wir am Donnerstag, dem 12.08.2021, endlich zum ersten Flug mit der Box starten. Es war ein voller Erfolg! In der Auswertung konnten wir erste Plots generieren. So wurden einige Vollkreise bei 100 km/h Fahrtmesseranzeige geflogen. Diese ließen sich auch in der Datenmenge wiederfinden.
Leider konnte die zweite Woche des Sommertreffens, in der die Breitenerprobung des Messsystems geplant war, nicht mit gutem Wetter punkten. Daher konnten leider keine weiteren Messflüge durchgeführt werden. Das ist zwar schade, aber kein Genickbruch, da die AK-8 schon darauf wartet die Messanlage in Rheinstetten auszuführen. Und wir freuen uns auch schon sehr darauf.
Die Daten des Sommertreffens geben uns bereits wichtige Informationen und zeigen auf wo wir das System weiter verbessern können.
In der Zukunft hoffen wir, dass wir den Messpod als Teil eines modularen Systems ohne spezifische Sensoren zulassen können. Dann könnten andere Forschungsgruppen auf uns zukommen und ihre Sensoren und Sonden einbauen lassen. Dies würde den Gruppen dabei helfen, dass sie bei der Erprobung ihrer Sensoren und Sonden nicht auf Drohnenflug zurückgreifen müssten. Außerdem gewinnt die Akaflieg Karlsruhe an Erfahrung.
Das Projektteam ist auf jeden Fall schwer begeistert vom Digital Zachering. Daher könnt ihr euch darauf freuen, bald von weiteren Fortschritten (und vielleicht auch Rückschlägen) zu hören.
Für Anfragen, Rückmeldungen und Anregungen schreibt gerne an: messpod@akaflieg-karlsruhe.de
Referenz:
B. Hall and T. Povey (2017). „The Oxford Probe: an open access five-hole probe for aerodynamic measurements.“ Measurement Science and Technology 28(3).
Da wir dieses Weihnachten nicht wie gewohnt in großer Runde genießen können, haben wir uns überlegt wie wir euch dennoch nah sein und für die ein oder andere weihnachtliche Backaktion sorgen können.
Daher wurden in hochwissenschaftlichen Teig-und Formerprobungen, Formen kreiert, denen die höchsten Standards in Design und Anwenderfreundlichkeit gerade gut genug sind!
Die Keksformen sind wirklich sehr gut!
Keks 2020
Herunterladen (und anschließend im 3D-Drucker drucken) könnt ihr die praktischen Helfer hier:
Wir wünschen euch sehr viel Freude mit den Ausstechern und würden uns wie verrückt über zahlreiche Bilder eurer Kreationen freuen!
Vielen Dank an Victor für die kreative Ausarbeitung der Formen:)
Einen großen Fertigungsaufwand an der AK-X stellen die unzähligen Metallteile dar die hauptsächlich in der Steuerung und den Fahrwerken verbaut sind. Bedingt durch die hohen Anforderungen übersteigen ebendiese Teile aber auch häufig unsere eigenen Fertigungsmöglichkeiten. Insb. CNC Fräs- und Drehteile können wir nicht selber fertigen. Umso dankbarer sind wir deshalb für Sponsoren, die uns bei diesen Teilen unterstützen.
Wassermann Technologie ist dabei zu einem sehr wichtigen Sponsoren für uns geworden, da uns die Firma mit einer Vielzahl an komplexen Fräs- und Drehteilen beliefern kann. Dabei setzen wir auf die jahrelange Erfahrung des Unternehmens in der CNC-Technik. Ende Mai hatten wir die Gelegenheit das Werk zu besuchen und die weitere Zusammenarbeit zu besprechen. Bei den anwesenden Maschinenbaustudenten waren die Fräszentren in der Größe eines Hauses Liebe auf den ersten Blick 😉
Viele fertige Teile konnten wir schon freudig in Empfang nehmen und einige Fertigungsaufträge laufen aktuell noch.
Wir freuen uns auf eine weiterhin so gute Zusammenarbeit!
Wir haben uns entschlossen, unseren Flugzeugpark um ein doppelsitziges Flugzeug vom Typ Twin II des Herstellers Grob Flugzeugbau zu erweitern. Genauer gesagt handelt es sich um Teile von insgesamt drei verschiedenen Flugzeugen dieses Typs. Das aus unserer Sicht unschlagbar günstige Angebot aus Dänemark wollten wir uns nicht entgehen lassen und haben daher quasi über Nacht Finanzierung und Transport der Flugzeugteile nach Karlsruhe organisiert.
Neben der Entlastung unseres Schulungsdoppelsitzers DG-1000 sind auch das Erlernen und die Weitergabe von Know-how im Bereich Flugzeugreparatur innerhalb der Akaflieg Ziele des Projekts.
Stand der Reparatur:
Der Twin mit dem Wettbewerbskennzeichen XNZ hat durch eine Außenlandung im Wasser Schäden an den Tragflächen erlitten. Der Rumpf ist bis auf kleine Beschädigungen jedoch intakt und in sehr gutem Zustand. Er soll nun, in Kombination mit einem anderen Flächenpaar, als erstes fliegen. Durch die Landung im Wasser mussten aus dem Rumpf alle Steuerstangen, die nicht aus Aluminium gefertigt sind, ausgebaut und auf Rost überprüft werden. Die Instrumente sowie die Schleppkupplungen wurden ebenfalls ausgebaut und zur Reparatur bzw Überholung zum jeweiligen Hersteller geschickt. Als nächstes gilt es, aus einem fertig geformten Haubenglas eine neue Haube auf den Rumpf anzupassen, und die bei der Landung zerstörte Fahrwerksverkleidung zu ersetzen. Am Holmtunnel ist leider eine etwas aufwändigere GFK-Reparatur notwendig.
Eine exakte Deadline für den Erstflug gibt es noch nicht, wir hoffen aber, dass die XNZ bereits in unserem Herbstschulungslager im Oktober geflogen werden kann.
Während letztes Jahr sehr viel an den Tragflächen und dem Rumpf der AK-X gearbeitet wurde, ist zeitgleich auch die Konstruktion und Auslegung der Fahrwerke vorangeschritten. Im Folgenden erfahrt ihr, welche Schritte notwendig waren um vom Konzept über die Konstruktion und Auslegung zu den fertigen Bauteilen zu kommen.
Konstruktion: Wie anfangen?
Mit der Konstruktion des Hauptfahrwerks wurde im Januar 2018 begonnen. Als erstes mussten wir alle Anforderungen und Randbedingungen sammeln und uns überlegen, durch welches Konzept wir alles gleichzeitig erfüllen können. Hauptaufgabe des Fahrwerks ist es, den Stoß bei der Landung zu dämpfen und ein sicheres Ausrollen des Segelflugzeugs zu gewährleisten. Zusätzlich galt es einige weitere Herausforderungen zu meistern: Das Fahrwerk sollte hydraulisch einfahrbar sein, eine variable Spureinstellung besitzen und natürlich möglichst leicht sein. Und dann ist weiterhin auch noch der Bauraum in unserem Nurflügler sehr begrenzt.
In den folgenden Monaten entwickelten wir die kinematischen und hydraulischen Konzepte, schätzten den Bauraum einzelner Teile ab und konstruierten schließlich alle Komponenten des Fahrwerks. An dieser Stelle noch einmal vielen Dank an Herrn Mayer, der uns mit Know-How und Hardware bei unserem Hydrauliksystem geholfen hat (Hydraulik Liftsysteme Walter Mayer GmbH). Nach einigen Iterationen stand die fertige Konstruktion: So fährt das Fahrwerk nach dem Start ein und vor der Landung aus.
3D-Druck: Rapid Prototyping
Um unsere Konstruktion abzusichern haben wir eine komplette Version unseres Hauptfahrwerks 3D-gedruckt und in den Fahrwerkskasten eingebaut. Wir waren dabei erstaunt, wie gut viele Teile passten, haben aber auch festgestellt, dass wir wegen kleiner Bauabweichungen im Fahrwerkskasten ein paar Teile anpassen müssen. Mit den 3D-gedruckten Teilen geht das denkbar einfach, nach kurzer Behandlung durch Bandsäge, Dremel und Schleifscheife haben endlich alle Teile gepasst und wir konnten die neuen Maße ins CAD übernehmen.
Das 3D-gedruckte Fahrwerk hatte neben dem Rapid Prototyping noch einen weiteren Nutzen: Auf der 90-Jahr-Feier der Akaflieg konnten wir unseren Prototypen auf eigenem Fahrwerk vorstellen. Eine zweite Version des 3D-gedruckten Fahrwerks konnten wir dann auf der AERO 2019 vorstellen.
Materialwahl: Stahl oder doch etwas Ausgefallenes?
Bei Segelflugzeugen bestehen die Fahrwerke meist aus Stahl, denn trotz seiner hoher Dichte ist der Werkstoff wegen der hohen Festigkeit ein ausgezeichneter Leichtbauwerkstoff.
Für unsere Konstruktion hatten wir zunächst auch Stahl vorgesehen, da er neben der Leichtbaugüte auch noch einfach zu beschaffen und im Vergleich zu den anderen Leichtbauwerkstoffen sehr günstig ist. Zudem sorgt die hohe Steifigkeit von Stahl dafür, dass auch dünne Streben nicht so schnell ausknicken können.
Während der Berechnung hat sich jedoch schnell herausgestellt, dass die hohen Belastungen an das Fahrwerk entweder den Einsatz von viel Material oder hochfestem Stahl notwendig machen würden. Da wir ein hohes Gewicht vermeiden wollten, haben wir also hochfesten Stahl als Konstruktionswerkstoff der meisten Teile gewählt. Weniger belastete Bauteile sollten aus Aluminium hergestellt werden. Hochfester Stahl hat jedoch das Problem, dass er sich nicht mehr so gut schweißen lässt. Zudem hätten wir jedes geschweißte Teil wärmebehandeln müssen.
Zeitgleich haben wir durch die Firma Wolf-Hirth die Möglichkeit angeboten bekommen Titan-Bauteile zu schweißen. Kurzerhand wurde die gesamte Konstruktion auf den Einsatz von Titan geprüft und es hat sich gezeigt, dass wir mit ein paar kleinen konstruktiven Änderungen bei fast jedem Bauteil Titan einsetzen können.
Der Materialwechsel führte zu einer Reduktion auf fast die Hälfte des ursprünglichen Gewichts. Ein weiterer Vorteil ist, dass wir uns das Lackieren ersparen können, da Titan im Gegensatz zu Stahl sehr korrosionsbeständig ist. Zudem hatten wir so die Möglichkeit neue Fertigungsverfahren zu nutzen, zum Beispiel bei der 3D-gedruckten Gabel des Bugfahrwerks.
Berechnung: Viele bunte Bilder
Nachdem die Konstruktion weitgehend abgeschlossen war, haben wir angefangen die Festigkeit unserer Bauteile zu berechnen. Die Berechnung war ein iterativer Prozess, bei dem wir immer wieder die Konstruktion an die vorgegebenen Lasten angepasst haben, bis diese zu einer möglichst gleichmäßigen Belastung aller Bauteile im Fahrwerk geführt haben.
Das war notwendig, da wir für unser Segelflugzeug die Sicherheit aller Teile gewährleisten müssen. Zudem möchten wir aber auch eine Überdimensionierung vermeiden und konnten so an vielen Ecken nochmal etwas Gewicht einsparen.
Die schönen bunten Bilder, die Abaqus ausgibt, müssen sinnvoll intepretiert werden: Wo sind Spannungsspitzen, die dem Bauteil langfristig schaden können? Wo ist noch Luft um Material zu sparen? Oder sollen wir doch einen anderen Werkstoff verwenden?
Fertigung: Jetzt gibts endlich Hardware
Nach über einem Jahr Konstruktion und Auslegung ist Anfang 2019 die Fertigung des Hauptfahrwerks angelaufen. Zunächst haben wir von allen Bauteilen technische Zeichnungen angefertigt und anschließend Unternehmen für die Fertigung kontaktiert. Die Firma Aircraft Philip hat die Fertigung unserer teilweise sehr komplexen Fräs- und Drehteile übernommen. An dieser Stelle wollen wir uns noch einmal für die großzügige Unterstützung bedanken. Einfache Bauteile haben die Konstrukteure und weitere Akaflieger selbst in unserer Werkstatt hergestellt. Einige Bauteile werden auch vom Institut für Strömungsmechanik am KIT gefertigt, vielen Dank nochmal insbesondere an Werkstattleiter Heiko Bendler und seine Azubis.
In den nächsten Wochen und Monaten gibt es noch Einiges zu tun, bis wir die Bauteile einbauen können. Viele der Frästeile sind die Knotenpunkte von Schweißkonstruktionen und müssen noch mit anderen Teilen und Halbzeugen zum fertigen Bauteil verschweißt werden. Dazu werden gerade bei uns in der Werkstatt Schweißgestelle gebaut, in denen die Teile zum Schweißen ausgerichtet werden. Nachdem die Bauteile verschweißt sind, können wir dann endlich anfangen unsere Fahrwerke in die AK-X einzubauen.